The Role of Copper in Today’s World
Copyright
The 2022 Definitive Guide to Copper, Its History, Uses, and More!—Copyright © 2022 by Jony Chen. All rights reserved. No part of this book may be reproduced or used in any form or by any means, electronic or mechanical, including photocopying, or recording, or by any information storage or retrieval systems, without permission in writing from the author or the publisher.
Legal Notice
Under no circumstances will I hold any blame or legal responsibility against the publisher, or the author, for any damages, reparations, or monetary losses for the information contained within this book, either directly or indirectly.
Disclaimer
Please note that the information contained within this document is for educational and entertainment purposes only. We have tried to present accurate, up-to-date, reliable, and complete information. No warranties, express or implied, are made by the author or the publisher. Readers acknowledge the author is not engaged in rendering legal, financial, medical or professional advice.
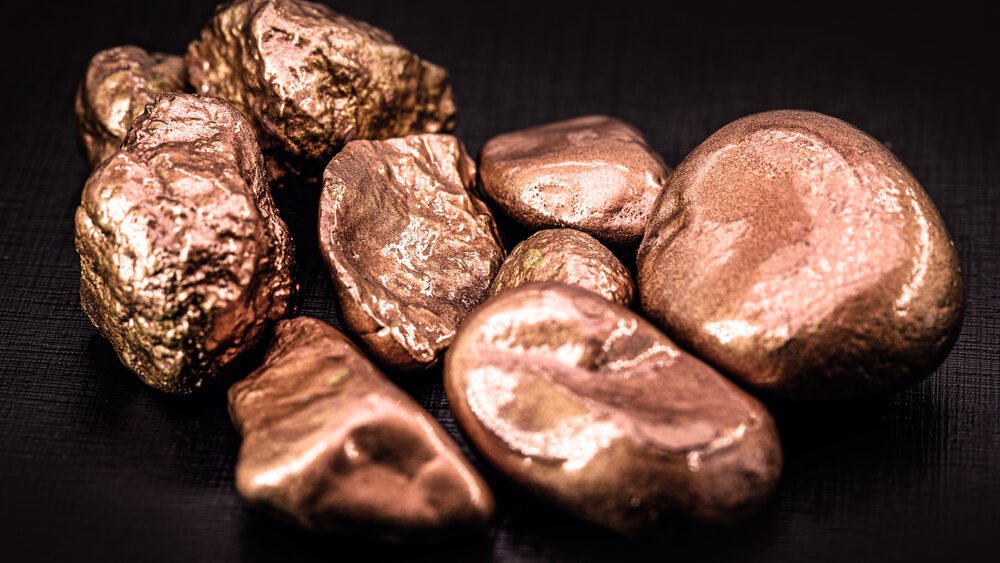
Introduction
This guide provides the reader with a broad overview and a working knowledge of copper. You have questions! Such as—What is copper used for? What is bronze and how does it differ from other metals? How can I decide when copper is the right choice for my purposes?
The answers to these questions and many others are provided in the pages that follow. For example, brass is an alloy of copper and zinc, the proportions of which can be varied to achieve certain properties.
In an era where credibility is in short supply, trust needs to be earned. Readers should be confident that I have expertise in this subject, having co-founded Gold Precision Co. Ltd. in 2012. Gold Precision is a metal stamping manufacturer that serves customer needs from prototyping to the final product, including stamping mold design, mold trial, processing and assembly.
This guide will allow you to make informed decisions regarding the products you buy, the material you use to manufacture your products, the material’s properties (including pros & cons), and other valuable insights.
The information in this guide will save you from making costly mistakes, so the sooner you read it, the better.

Chapter One: Copper—A Brief History and Overview
Copper, also known as cuprum, appears in the periodic table of elements as Cu, and bears the atomic number, 29. It melts at 1083° Centigrade. Around 8000 BCE, Neolithic (stone age) peoples began using this reddish brown metal to replace their stone tools. Naturally, they were using copper found in its native state, because smelting from copper bearing ores was not practiced until some 4000 years later, when smelting was discovered in Mesopotamia.
By 3000 BCE, people had learned to alloy copper with tin, which resulted in bronze and the beginning of the Bronze Age.
Copper is easy to stretch, simple to mold (cast), and readily shaped. Copper forms copper oxide on its surface, which helps it resist further corrosion. You have probably seen roofs on older buildings that appear bluish-green. These are copper roofs and the bluish-green patina is copper oxide.
While copper doesn’t make the top ten list in terms of abundance, there is certainly no shortage. The world’s top five copper suppliers produced almost 12 million metric tons of copper in 2016, led by Chile, with 5.5 million metric tons, Peru, with 2.3 million, China, with 1.74 million, the United States, with 1.4 million and Australia, with 0.97 million. Worldwide, over 19 million metric tons of copper were produced in 2016. Today’s figures, although unavailable, likely exceed those impressive numbers.
Copper was critical to human development, and continues to be the metal of choice for a vast array of home, industrial, and high technology applications. This explains the increased demand copper has enjoyed in the past three decades. This demand increases as emerging economies grow and develop. China, for example, has already eclipsed the United States as the world’s leading copper consumer, quadrupling its consumption rate in the 12 years following 2000.
Why Is Copper in Such Demand?
The attractive and unique properties of copper are responsible for its high demand. For example, only silver exceeds copper’s electrical conductivity. Many think gold is the best conductor, but silver and copper rank first and second, respectively. The only advantage gold holds over silver and copper is its corrosion resistance.
Copper is second only to silver in heat conductivity. For this reason, copper is the preferred metal for high-end cookware. As I write this, copper is selling for $0.28 per ounce, while silver is selling for $23.78 per ounce. Imagine the price tag for a 2 quart Dutch oven made from silver!
Because copper has excellent electrical and thermal conductivity, and is low in cost compared to other metals with similar properties, demand for copper is high.
Copper’s ability to alloy easily with other metals contributes to the high demand for this metal. It is often combined with other metals, such as zinc (to form brass), tin (to form bronze), or nickel. These alloys have desirable characteristics and, depending on their composition, are developed for highly specialized applications. For example, in the maritime industry, the hulls of ships are skinned with a copper-nickel alloy because it resists corrosion in seawater and discourage barnacles from adhering to the ship’s hull, which reduces drag and increases fuel efficiency. Brass is more malleable and has better acoustic properties than pure copper or zinc; consequently, it is used in a variety of musical instruments, including trumpets, trombones, and cymbals.
Copper in Our Everyday Lives
The unique and varied properties of copper have ensured that this metal is fully integrated with our daily existence. When we turn on a light, the electricity that illuminates it flows through copper wires. Powering up almost any electrical appliance or device depends on copper, from the power cord to your appliances, to the circuit boards in your smartphone or tablet, to the electric motor in your washing machine—copper is silently, invisibly making these wonderful inventions work efficiently, and at a lower cost than would otherwise be possible.
Art, in the form of sculptures, decorative flourishes, in jewelry as a base metal onto which gold or silver is plated, and medicinally, in the form of anti-arthritic bracelets, germ killing door knobs, handrails and pulls, all use this miracle metal.
In the animal kingdom, the blood of many aquatic creatures is copper, rather than iron based. Such creatures as the octopus, crab, lobster and shrimp rely on the copper in their bloodstreams to deliver life-giving oxygen to the cells of their bodies.
Now that you have been exposed to some history, and some key properties of copper, the next chapter will discuss the various alloys of copper, their uses, and their importance to our daily lives.
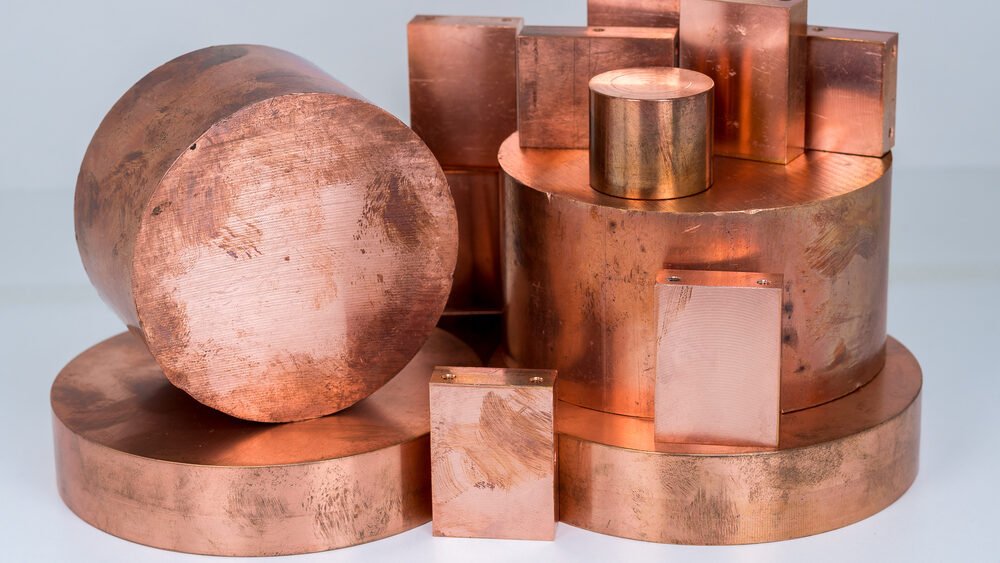
Chapter Two: Bronze, Brass, & the Lesser Known Copper Alloys
Let’s begin this chapter with a definition—a copper alloy is a metal, principally consisting of copper combined with small amounts of other metal or metals. The combination of copper with one or more additional element(s) is defined as a copper alloy, the most common of which are bronzes and brasses.
Bronze Alloys
We will start with bronze, because it is not only well known, it is also the first copper alloy to be discovered, an alloy of copper & tin. It is no surprise that the discovery of tin around 3000 BCE coincides with the onset of the bronze age.
The proportions of copper and tin vary from 67 percent copper to 95 percent copper. Copper to tin ratios yield bronze alloys with specific properties. For example, the bronze alloy used for bells contains 20 to 25 percent tin, whereas the bronze alloy used in casting statues contains less than 10 percent tin. Most bronze alloys melt at a lower temperature than copper alone—around 913° Centigrade.
All bronze alloys, regardless of composition, are harder, have greater durability, and higher corrosion resistance than does copper or tin alone. It may surprise you to learn that bronze is actually harder than pure iron, and significantly more resistant to corrosion. The Iron Age did not occur because a superior metal had been discovered. The Iron Age came about because of the abundance of iron compared to copper. Iron was widely available at low cost, and that is what actually triggered the Iron Age.
There are six main classes/families of bronze
- Tin bronzes (aka phosphor bronzes)
- Copper nickel bronzes
- Aluminum bronzes
- Silicon bronzes
- Lead bronzes
- Manganese bronzes
Cast alloys are poured into a mold after they are created, while wrought alloys are worked in their solid form by rolling, stamping, bending, extruding, etc. The following table displays the UNS numbers for wrought and cast alloys.
Broadly speaking, all copper and its alloys are identified by unified numbering system (UNS) designations.
Wrought Alloys
Copper | C 10100 – C 15999 |
High Copper Alloys | C 16000 – C 19999 |
Brasses | C 20000 – C 49999 |
Bronzes | C 50000 – C 69999 |
Copper Nickels | C 70000 – C 73499 |
Nickel Silvers | C 73500 – C 79999 |
Cast Alloys
Copper | C 80000 – C 81399 |
High Copper Alloys | C 81400 – C 83299 |
Brasses | C 83300 – C 89999 |
Bronzes | C 90000 – C 95999 |
Copper Nickels | C 96000 – C 96999 |
Nickel Silvers | C 97000 – C 97999 |
Leaded Coppers | C 98000 – C 98999 |
Special Alloys | C 99000 – C 99999 |
These begin with C10100 and end at C 99999. For example, C 93200 is an alloy commonly used for bearings.
Other designators exist, such as SAE, ASTM, and more. Detailed information on UNS and other designations are readily available on the Internet and so will not be addressed within the pages of this book.
Brass Alloys
Brass, predominantly an alloy of copper and zinc, is bright gold, reddish gold, or silver, highly malleable, tarnish resistant, easily machined, and melts at around 927° Centigrade, a temperature lower than is needed to melt copper.
It is believed that brass was discovered around 500 BCE, much later than bronze. Zinc, unlike tin, was not readily available in its native state, and it is difficult to make. Zinc melts at just 420° Centigrade and literally boils at 950° Centigrade.
The only way to make brass in those days was by heating smithsonite (calamine) and copper together in a crucible. The zinc vapor was absorbed by the copper and formed brass. A subsequent melt gave the brass uniformity.
Brass contains various ratios of copper and zinc, with zinc content ranging from 11 to 28 percent. At 18 percent zinc, the Romans called it aurichalum, and they used it for helmets because of the gold color. Brass was also used for jewelry and other forms of ornamentation. The Romans also used brass in their coinage, particularly the coin known as the sesterces.
Most brass alloys share the following traits…
- Ductility
- Conductivity
- Machinability
- Hardness
- Strength
- Corrosion resistance
- Wear resistance
- Recyclability
These properties make brass indispensable in a variety of industries that make components requiring a lengthy service life at low cost. Brass, for example, tops the list in the electrical industry.
While there are at least 60 types of brass, they can be grouped into three basic classes/families…
- Copper-zinc brasses
- Leaded brasses
- Tin brasses
As I mentioned previously, all copper and its alloys are identified by unified numbering system (UNS) designations.
Lesser Known Alloys
Were you aware that there are at least 60 types of brass, and an even greater number of bronzes? There are also several copper alloys made with silver and/or gold. These precious, and occasionally exotic, metal alloys are not commonly known, and include…
- Auricupride—This alloy occurs in nature and it results from combining copper and gold.
- Guanin—A pre-Columbian alloy of Copper (25%), Gold (56%) and Silver (18%). Reddish, with a brilliant shine, it is purported to have supernatural powers.
- Electrum—Also known as green gold, this alloy is comprised of Copper (6 to 20%) Gold (75 to 90%), and Silver (0 to 15%).
- Rose, Red, and Pink Gold—These golds are actually alloys of copper (20 to 50%), gold (50 to 75%) and silver (0 to 5%), with the varying percentages governing the eventual color of the metal.
- Shakudo—An alloy that combines copper (90 to 96%) with gold (4 to 10%).
- Spangold—Yet another alloy of copper (18 to 19%), gold (76%), and aluminum (5 to 6%).
These are just a few examples—there are many other copper alloys. The point being, copper is an extremely versatile element and can be alloyed in countless ways.
In this chapter, we have primarily focused on bronze and brass, offering insights into their composition, uses, and a little of the history behind them.
The next chapter will teach you about the strengths, mechanical, and other properties of bronze and brass alloys.
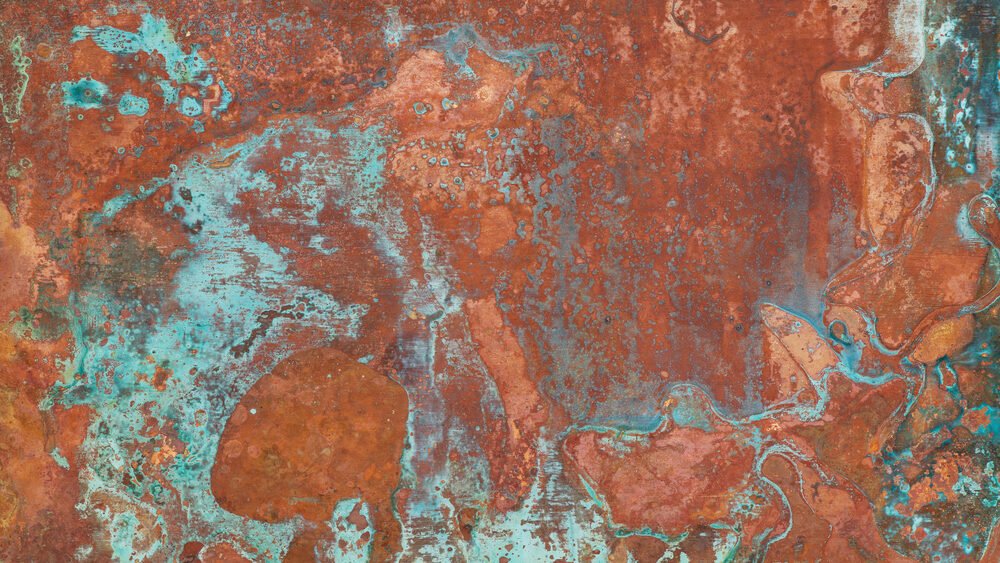
Chapter Three: Bronze & Brass—Strengths, Mechanical and Other Properties
Bronze and brass share many strengths, mechanical and other properties, as you will learn in the following pages. Bronze resists corrosion and metal fatigue, conducts heat and electricity, and more, as you will learn in this chapter.
As you learned in Chapter Two, there are many bronze and brass alloys, each identified under the UNS system. Each alloy has its own characteristics, in terms of strength, mechanical, and other properties. The specific characteristics of a given alloy are identified by the unified numbering system (UNS) as discussed in Chapter Two. It is the UNS that should be used to determine with specificity what the characteristics a given alloy may be.
What follows below are the strengths, mechanical, and other properties that can be found in bronzes overall, and do not reflect the characteristics of a specific alloy.
Items | Metal(DIN/UNS) | Properties(Conductivity) | Applications |
Copper | OFE-Cu/C10100 | Conductivity %IACS 101 | submarine fibre optic cables coaxial cables and waveguides Leadframe for semiconductors Vacuum Technology Heat Sinks |
Copper | Cu-OF/C10200 | Conductivity %IACS 100 | submarine fibre optic cables coaxial cables and waveguides Leadframe for semiconductors Vacuum Technology Heat Sinks |
Copper | Cu-PHC/C10300 | Conductivity %IACS 98 | Standard material for longitudinally welded cables Components for the electrical industry |
Copper | CU-DHP/C12200 | Conductivity %IACS 99.9 | Apparatus industry Leadframe for power semiconductors Cable strips |
Copper | Cu-ETP/C11000 | Conductivity %IACS 100 | Main materials for general electrical applications Stamped parts Transformer coils Cable strips Heat Sinks |
Brass | CuZn5/C21000 | Conductivity %IACS 57 | Jewellery and metal goods Components for the electrical industry |
Brass | CuZn10/C22000 | Conductivity %IACS 43 | Jewellery and metal goods Components for the electrical industry Leadframe |
Brass | CuZn15/C23000 | Conductivity %IACS 36 | Jewellery and metal goods Components for the electrical industry Cladding panels |
Brass | CuZn20/C24000 | Conductivity %IACS 33 | Jewellery and metal goods Deep drawn parts |
Brass | CuZn30/C26000 | Conductivity %IACS 28 | Jewellery and metal goods Components for the electrical industry Deep drawn parts Stamped parts Connectors |
Brass | CuZn33/C26800 | Conductivity %IACS 28 | Jewellery and metal goods Components for the electrical industry Deep drawn parts Stamped parts Connectors |
Brass | CuZn36/C27000 | Conductivity %IACS 26 | Metal goods Deep drawn parts Stamped parts Connectors |
Brass | CuZn37/C27200 | Conductivity %IACS 26 | Metal goods Deep drawn parts Stamped parts Connectors Components for the electrical industry |
Brass | Conductivity %IACS 26 | Connectors Components for the electrical industry Stamped parts | |
Free Machining Brass | CuZn38Pb2/C35000 | Conductivity %IACS 24 | Precision mechanical componets Watch and clock parts Milled parts |
Free Machining Brass | CuZn39Pb2/C37700 | Conductivity %IACS 24 | Precision mechanical componets Watch and clock parts Milled parts |
Special Brass | CuSn3Zn9/C42500 | Conductivity %IACS 28 | Components for the electrical industry Connectors |
Special Brass | CuZn23Al3Co/C68800 | Conductivity %IACS 17 | Components for the electrical industry Contact springs Insulation displacement connectors |
Phosphor Bronze | CuSn4/C51100 | Conductivity %IACS 22 | Stamped parts Connectors Contact springs |
Phosphor Bronze | CuSn5/C51000 | Conductivity %IACS 19 | Stamped parts Connectors Contact springs |
Phosphor Bronze | CuSn6/C51900 | Conductivity %IACS 16 | Stamped parts Connectors Contact springs |
Phosphor Bronze | CuSn8/C52100 | Conductivity %IACS 13 | Stamped parts Connectors Contact springs Relay Springs Slide bearings |
Nickel Silver | CuNi12Zn24/C75700 | Conductivity %IACS 8 | Deep drawn parts Connectors Contact springs Cutlery |
Nickel Silver | CuNi18Zn27/C77000 | Conductivity %IACS 6 | Connectors Relay Springs Electrical contacts |
Nickel Silver | CuNi18Zn20/C76400 | Conductivity %IACS 6 | Connectors Relay Springs Shieldings |
Nickel Silver | CuNi12Zn25Pb1/C79200 | Conductivity %IACS 8 | Keys for automotive industry Keys for high security cylinders Musical instruments Watch components |
CuNi-Alloys | CuNi9Sn2/C72500 | Conductivity %IACS 11 | Relay Springs Connectors |
Berry Alloy | CuBe2/C17200 | Conductivity %IACS 20 | Connector Plugs Switches Relays Motor parts EMI shielding springs Temperature controlers |
Berry Alloy | CuNi2Be/C17510 | Conductivity %IACS 50 | Connector Plugs Relays EMI shielding springs Temperature controlers |
High-performance alloys | CuNi3SiMg/C70250 | Conductivity %IACS 43 | Components for the electrical industry Stamped parts Relay Springs semiconductor components Connector suitable for elevated temperatures |
High-performance alloys | CuNi1Co1Si/C70350 | Conductivity %IACS 50 | Components for the electrical industry Stamped parts Relay Springs semiconductor components Connector suitable for elevated temperatures |
High-performance alloys | CuFe2P/C19400 | Conductivity %IACS 64 | Components for the electrical industry Stamped parts Connectors Leadframes for semiconductors |
High-performance alloys | CuCrSiTi/C18070 | Conductivity %IACS 78 | Components for the electrical industry Stamped parts Relay Springs semiconductor components Connector suitable for elevated temperatures |
High-performance alloys | CuNiSiP/C19010 | Conductivity %IACS 50 | Components for the electrical industry Stamped parts Relay Springs Connectors |
High-performance alloys | CuFe0,1P/C19210 | Conductivity %IACS 91 | Components for the electrical industry Leadframes for power transistors Connectors |
High-performance alloys | CuSn0,15/C14415 | Conductivity %IACS 88 | Components for the electrical industry Connector pins Fuse boxes in automobiles Leadframes for semiconductors |
High-performance alloys | CuCrAgFeTiSi/C18080 | Conductivity %IACS 50 | Components for the electrical industry Stamped parts Relay Springs Connector suitable for elevated temperatures |
Bronze – Mechanical Properties
- Yield Strength
The yield strength of bronze is 125 mega-pascals (MPa), about one-half that of stainless steel.
Cold working and hot working increases yield strength.
- Ductility
The inherent properties of cold & hot working, plus its ductility\elongation, make bronze fairly easy to fabricate.
Ductility is the amount of material will stretch before breaking. This is determined during tensile testing. Bronze elongation is in the 20 percent range. To put this in some perspective, stainless steel falls in the 60 to 70 percent range.
- Hardness
Hardness is the penetration resistance of the substance surface. Hardness tests evaluate the depth that a ball or cone-shaped object can be pressed into the surface of a material. The Brinell scale uses a 10 millimeter hardened steel ball to measure the width of the indentation, while the Rockwell method uses a diamond cone and measures depth of penetration.
Bronzes can be hardened by via hot and cold working. As previously noted, bronze is actually harder than pure iron.
- Tensile Strength
Typically, tensile strength is the only mechanical characteristic needed to define wire and bar and products. Similar substance types may be used at different tensile strengths for entirely different applications. The required tensile strength of wire and bar products directly related to the product’s final use, post fabrication.
Spring wire has the greatest tensile strength after fabrication. This strength is achieved by cold working the metal into rolled-up springs. The wire would not function as a spring without this great strength.
These high tensile strengths are not needed in wire used in forming or weaving processes. Bar or wire, used as the raw material for fasteners, such as screws and bolts, should be smooth enough shape into a head and threads, yet sufficiently strong to perform its intended function.
Bronze alloys have a range of yield and tensile strengths, with tensile strengths as high as 550 MPa.
- High Temperatures
The high temperature resistance of bronze does not compare favorably to the performance of carbon steels at high temperatures. Bronze is much less fire resistant, and will not keep its stiffness in high temperature conditions.
- Cryogenic Resistance
Bronze does not excel at dealing with broad temperature ranges, and cryogenic temperatures are poorly tolerated.
- Higher Work Hardening Ratios
The ability of a metal to increase its strength during the cold working process is possible with bronzes which can be cold and hot worked to enhance its strength.
- Electrical Conductivity and Permeability
Bronze, like all metals, conducts electricity. Its electrical conductivity, however, is not as good as brass.
Bronze is non-magnetic.
Bronze does not spark, giving it an advantage in combustible environments.
Bronze’s Chemical Properties
Bronze has unique chemical properties.
- Oxidation Resistance
Bronze is resistant to further oxidation after acquiring its patina of copper-oxide. When the patina has formed, further oxidation halts.
It does not need to be guarded by anti-corrosion coatings, such as paint, and should the patina wear away, it quickly forms a new coat, which provides continuous corrosion resistance.
- Biologically Inert
Bronze can react with biological material, making it a poor choice for medical use. This is because of its copper content. Copper is involved in over 300 biological functions in human beings.
- Acid and Base Resistance
Some types of bronze are resistant to a significant number of chemical compounds, acids and bases. Resistance differs from type to type, with some being highly resistant and other only resistant to low acidic or basic concentrations.
For example, bronze resists saltwater corrosion, and can survive in harsh environments for a longer period than some other metals.
Other Properties (besides physical and chemical properties)
Characteristics are not limited to chemical and mechanical ones. The list below highlights other properties that make bronze a great choice for many other applications.
- Recyclability
Bronze is highly recyclable, making it an excellent choice for manufacturing new products. This reduces the strain on the environment by lowering waste and minimizing the exploitation of new raw materials.
- Easy to Work
Bronze is very workable, allowing designers to create complex products and shapes. Bending, laser cutting, and CNC machining services, are all possible, with no need for exotic equipment.
- Easy to Maintain
Bronze products are readily cleaned, which can keep them looking new and extend their service life.
- Aesthetic Appeal
Bronze can achieve a high luster, or a beautiful patina, so this metal is an excellent choice for highly visible surfaces, and it can be engraved, tinted, embossed, and brushed.
Brass – Mechanical Properties
What follows below are the strengths, mechanical, and other properties that can be found in brasses overall, and do not reflect the characteristics of a specific alloy.
- Yield Strength
The yield strength of brass is around 140 Mpa.
Cold & hot working can boost yield strength. For example, tempered spring wire can be cold and hot worked to increase the yield strength.
- Ductility
The inherent properties of cold and hot work hardening, combined with the high ductility\elongation properties of brass, make it very easy to fabricate. These characteristics make brass ideal for deep drawing.
Ductility is the amount of material will stretch before breaking and is determined through tensile testing. Brass alloys have very good elongation statistics, which is one reason so many find it suitable for general applications. It is malleable, easy to cast, relatively inexpensive, and low-friction.
- Hardness
Hardness is the penetration resistance of the substance surface. Hardness tests evaluate the depth that a ball or cone-shaped object can be pressed into the surface of a material. The Brinell scale uses a 10 millimeter hardened steel ball to measure the width of the indentation, while the Rockwell method uses a diamond cone and measures depth of penetration.
Brasses can achieve a level of hardness via cold and hot working.
- Tensile Strength
Typically, tensile strength is the only mechanical characteristic needed to define wire and bar and products. Similar substance types may be used at different tensile strengths for entirely different applications. The required tensile strength of wire and bar products directly related to the product’s final use, post fabrication.
Spring wire has the greatest tensile strength after fabrication. This strength is achieved by cold working the metal into rolled-up springs. The wire would not function as a spring without this great strength.
These high tensile strengths are not needed in wire used in forming or weaving processes. Bar or wire, used as the raw material for fasteners, such as screws and bolts, should be smooth enough shape into a head and threads, yet sufficiently strong to perform its intended function.
Brasses have a broad range of yield and tensile strengths.
- High Temperatures
Brass does not fare well at high temperatures. Brasses are not fire resistant, and will not retain their stiffness.
- Cryogenic Resistance
Some brasses do well in the lower temperature ranges. Brass can keep its high tensile strength and exhibit toughness at low temperatures, extending its range of use, and opening up new possibilities for modern applications.
Cryogenic temperatures, however, are beyond the ability of brass to withstand.
- Higher Work Hardening Ratios
The ability of a metal to increase its strength during the cold working process is a property shared with brass, which can be cold and hot worked to improve its strength.
Spring wire is an excellent example.
- Electrical Conductivity and Permeability
Brass, like all metals, conducts electricity, although its electrical conductivity is poor compared to other metals such as copper, gold, and mercury. It is, however, a better conductor than bronze.
Brasses are non-magnetic.
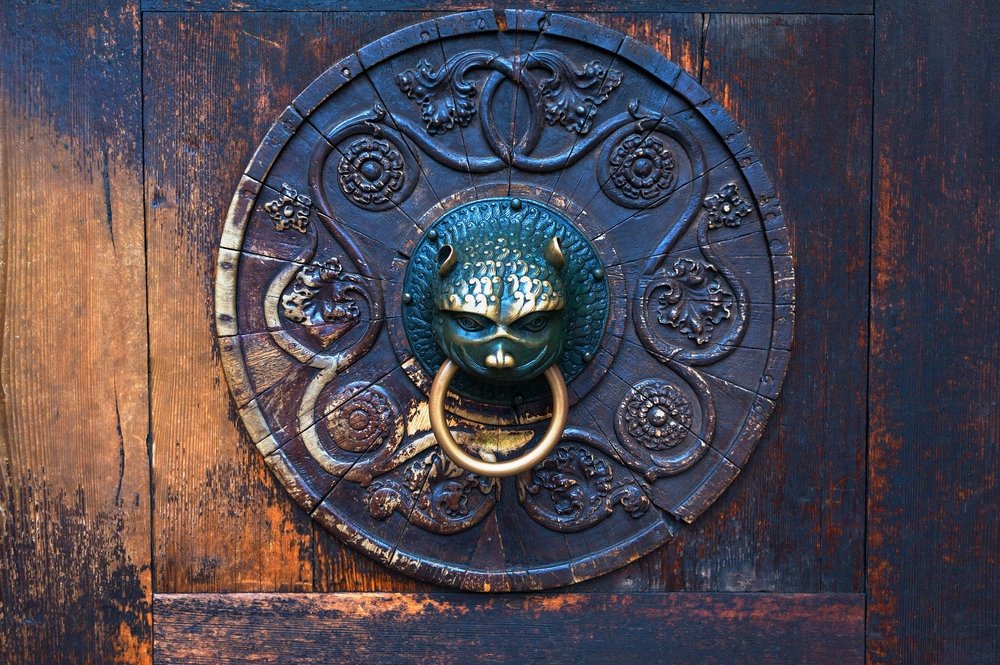
The Chemical Properties of Brass
Brass has some useful chemical properties.
- High Oxidation Resistance
Brass does not rust as it contains no iron. It does, however, oxidize. This oxidation occurs because of its copper content. Unlike iron, the oxidation only occurs on the surface, forming a patina which protects the underlying brass from further deterioration.
While some metals must be guarded by anti-corrosion coatings, such as zinc, or paint brass reacts to any damage or wear to its thin patina of oxide by forming a new coat, which provides continuous corrosion resistance.
- Biologically Inert
Brass can react with biological material, making it a poor choice for the medical field. Brass is anti-microbial, however, which makes it ideal for surfaces found in the healthcare industry.
Furthermore, brass (and bronze) contains a large amount of copper, which is known to be involved in over 300 biological processes.
- Acidic, Basic, And Organic Resistant
Brass is not resistant to organic compounds, acids and bases. Acid resistance is poor in all types.
Brass is not resistant to saltwater, moisture, and chloride compounds.
- Recyclability
Brass is highly recyclable, making it an excellent choice for manufacturing new products, without straining the environment. Using brass can reduce waste and minimize the need to exploit raw materials.
It’s non-biodegradable, which stops it from polluting. It does not break down and seep into the water table.
- Easy to Work
Brass is very workable, allowing designers to create complex products and shapes. Bending, laser cutting, and CNC machining services, are all possible, with no need for exotic equipment.
- Easy to Maintain
Brass is easily cleaned, which keeps it looking new and extends its service life. To preserve brass, take care to avoid exposure to chloride ions, such as in seawater. Some cleaning solutions can de-zincify brass as well.
This reduces replacement costs and makes an initially expensive purchase economical over time.
In businesses where hygiene standards are elevated, brass is often used. Brass is considered hygienic. This means it possesses antimicrobial properties and kills microorganisms after hours of contact with the alloy. This makes it a popular component in the healthcare industry.
- Aesthetic Appeal
Brass can achieve a high luster, so this metal is an excellent choice for highly visible surfaces. It can be engraved, tinted, embossed, and brushed.
In the next chapter, you will learn what elements are used as alloys to achieve these chemical, mechanical, and other properties.
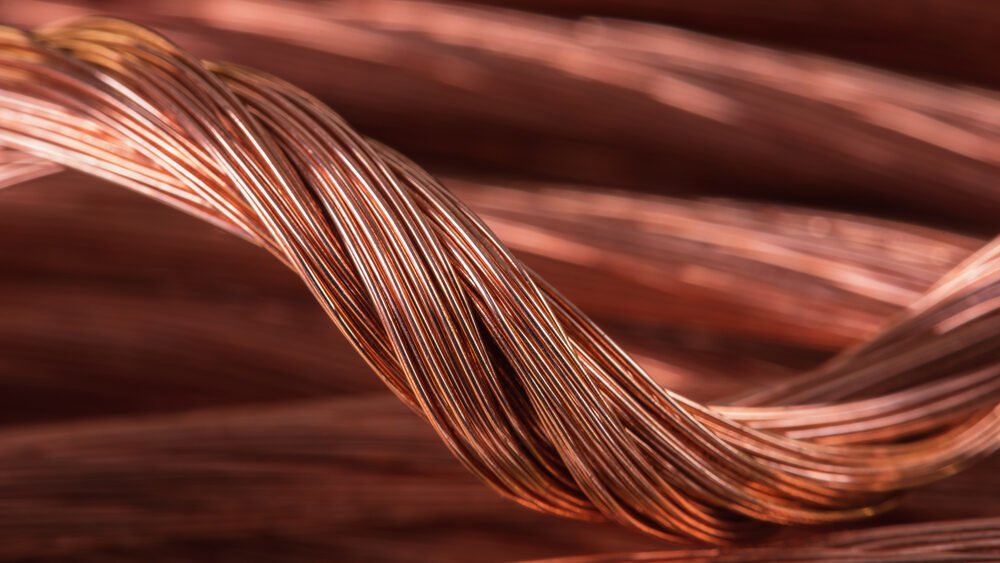
Chapter Four: Which Elements Create the Properties of Bronze & Brass
Various elements play crucial roles in the way bronze and brass perform in terms of strength, mechanical, and chemical properties. You have already learned that the various copper alloys are given a UNS designation based upon the composition of the alloy. The following text identifies those elements and explains the role played by each element.
The Elements
- Lead
Lead has been historically added to both bronze and brass alloys to improve machinability and it act as a solid lubricant. However, with recent developments in the negative health implications of lead, free machining coppers, brasses and bronzes are being transitioned to contain sulfur or tellurium instead of lead.
Brass can contain up to 3.5 percent lead. Lead enhances the machinability of brass and seals shrinkage pores, which helps the metal remain tight in pressurized environments such as water valves. The addition of lead does not alter the crystalline structure of brass.
Free machining brasses and free cutting brasses, such as C 36000 and C 38500, contain between up to 4.5% lead and have excellent hot forming properties.
- Manganese
Manganese is used in bronze (2.5 to 5 percent) to give it superior strength and corrosion resistance. With a yield strength of 460 MPa, manganese bronze surpasses the strength of some aluminum and low carbon steel alloys.
Manganese is added to brass (about 1.2 percent) to enhance its tensile strength, as high as 689 Mpa, and, depending on temper, its yield strength to as high as 683 Mpa. This type of brass has good formability, but unfortunately, this diminishes its machinability.
Manganese brasses such as C 86300 and C 86675 can also be classified as a type of bronze. They are high strength alloys with good torsional properties and corrosion resistance.
- Nickel
The addition of nickel (around 30 percent) results in nickel bronze, which is one of the two most common bronzes, the other being phosphor bronze. Two examples of nickel bronzes are cupronickel and nickel silver. Cupronickel is 70 percent copper and 30 percent nickel, whereas nickel silver is 60 percent copper, 20 percent nickel and 20 percent zinc. No silver! That is a reference to the color. Nickel silver is also known as German silver and as Maillechort.
Nickel is also alloyed with brass, producing a brilliant silver color, and a corrosion resistant metal. The United Kingdom’s one-pound coin is made from nickel silver containing 70 percent copper, 24.5 percent zinc, and 5.5 percent nickel.
- Copper
Copper is, of course, the main component of bronze and brass. Copper can also be added to other alloys, such as stainless steel, to produce properties such as precipitation hardening or enhanced corrosion resistance, predominantly in seawater and in the presence of sulfuric acid.
- Phosphorus
Bronze has an entire family built around phosphorus called phosphor bronze. These bronzes have a tin content of 0.01 to 1.0 percent, and a phosphorus content of 0.01 to 0.35 percent. Phosphor bronzes, also known as tin bronzes, have a fine grain, are durable, strong, and fatigue resistant, with a low coefficient of friction. Tin increases tensile strength and corrosion resistance, while phosphorous increases wear resistance.
Brass, on the other hand, incorporates phosphorus to enhance machinability.
- Sulfur
Added in small amounts through a process known as sintering, sulfur also improves machinability in both bronze and brass.
- Silicon
Silicon is typically used as a deoxidizing agent is present bin small quantities in some bronze and brass alloys.
For example, C 87850 and C 69300 are lead free brasses which use silicon to enhance machinability.
- Arsenic
Used in arsenical bronzes, arsenic adds a silvery sheen, results in a stronger metal, and provides superior casting qualities.
Small quantities of arsenic are present in some brass alloys allow to inhibit corrosion. C 26130, one example of this type, known as arsenical brasses.
- Aluminum
There is a family of aluminum bronzes containing aluminum in the 6 to 12 percent range. Aluminum bronzes are also alloyed with iron 6 percent (maximum), and nickel at 6 percent maximum. These bronzes are corrosion resistant and often used in marine related products, such as sleeve bearings and pumps or valves that handle corrosive liquids.
Brass contains a small amount of aluminum (5 percent), to give it a bright golden color—it is called section brass. European Union 10, 20, and 50 cent coins are made of this brass, and they refer to it as “Nordic gold.”
- Tin
Bronze is the metal formed when combined with copper, typically in a 70 percent copper, 30 percent tin ratio.
Brass types, such as C 43500, contain tin to decrease the effect of dezincification and enhance corrosion resistance.
- Zinc
Some percentage of zinc is used in certain types of bronze, but as we know, zinc is the element combined with copper to make brass.
- Iron
Iron can be found as an alloying element in aluminum bronzes.
Brass is sometimes alloyed with iron in small quantities to increase strength and hardness. Sometimes referred to as Aich’s metal, such brasses are sometimes used in marine applications.
There you have it! The dirty-dozen of elements used in creating bronzes and brasses.
In the next chapter, you will learn the advantages these elements provide bronze and brass in the marketplace.
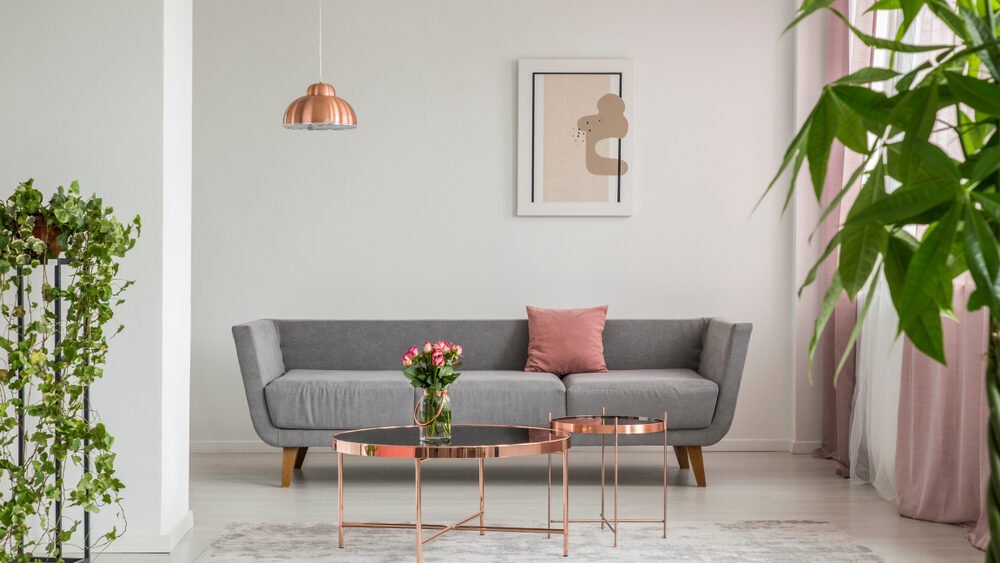
Chapter Five: The Characteristics and Advantages of Bronze & Brass
Bronze and brass are widely used in a variety of industries because they have a multitude of highly desirable features.
These attributes are made possible by adding various elements to copper, which, as we know, creates bronze, brass and other copper alloys.
Other desirable features for customers are its durability and strength, resistance to low and high-temperatures, ease of fabrication and high formability. Bronze and brass are long-lasting, low maintenance, attractive in appearance, recyclable, and environmentally friendly. Neither bronze nor brass needs to be coated, treated, or painted. The following list highlights the principal characteristics of bronze and brass.
- Corrosion resistant
- Good tensile strength
- Durable
- Only brass is anti-microbial
- Easy to form & and fabricate
- Low-maintenance
- Long service life
- Excellent aesthetics
- Recyclable & environmentally friendly
Top 7 Benefits of Bronze
Bronze offers a multitude of benefits, such as corrosion resistance, strength, ease of fabrication, and so on. Let’s get into greater detail.
- Oxidation Resistance
Bronze will oxidize because the copper in bronze fosters the formation of copper oxide. As I’ve mentioned previously, this oxide only forms on the metal’s surface and prevents further corrosion from occurring.
- Aesthetic Appearance
Bronze offers wonderful aesthetic, especially because of the patina.
- Ease of Fabrication
Modern methods permit bronze to be bent, cut, welded, machined, formed, and assembled more readily than other metals.
- Hardness
Some bronze alloys are harder that iron and much less brittle.
- Long-Term Value
When considering costs, production, material, and life cycle expenses, needs to be considered. When these are considered, bronze often comes out on top.
- Recyclable
Bronze is 100 percent recyclable, good for the environment and sustainable.
- Durability
Bronze is robust. Frequently used on ships because of its saltwater corrosion resistance, it is a durable metal.
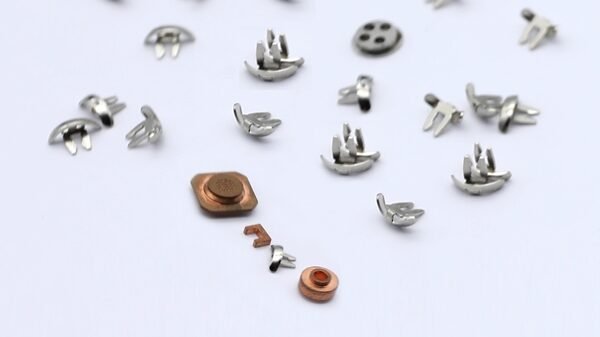
Top 7 Benefits of Brass
- Available in Many Shapes and Forms
Brass is available in bars, sheets, rods, plates, tubes, and pipe.
- Capable of accepting a Variety of Finishes
Brass can be knurled, brushed, and polished. It can be tinted, lacquered, and antiqued. It can have a satin or brushed finish, and can even be colored.
- Recyclable
Brass is also 100 percent recyclable, good for the environment, and sustainable.
- Ease of Fabrication
Brass is highly formable and malleable, allowing it to be bent, cut, machined, formed, and assembled more readily than other metals. This is a particular excellent feature for deep draw stamping.
- Rust Resistant
Brass, like bronze, can also form a protective patina of copper oxide.
- Easily Maintained
Brass can be maintained easily using Brasso, or a similarly formulated cleaning product.
- Anti-microbial
Brass (and silver) has proven anti-microbial properties, making it ideal for high-traffic areas—used for door knobs, hand rails, etc. Brass is a particularly prized in the healthcare industry for this property.
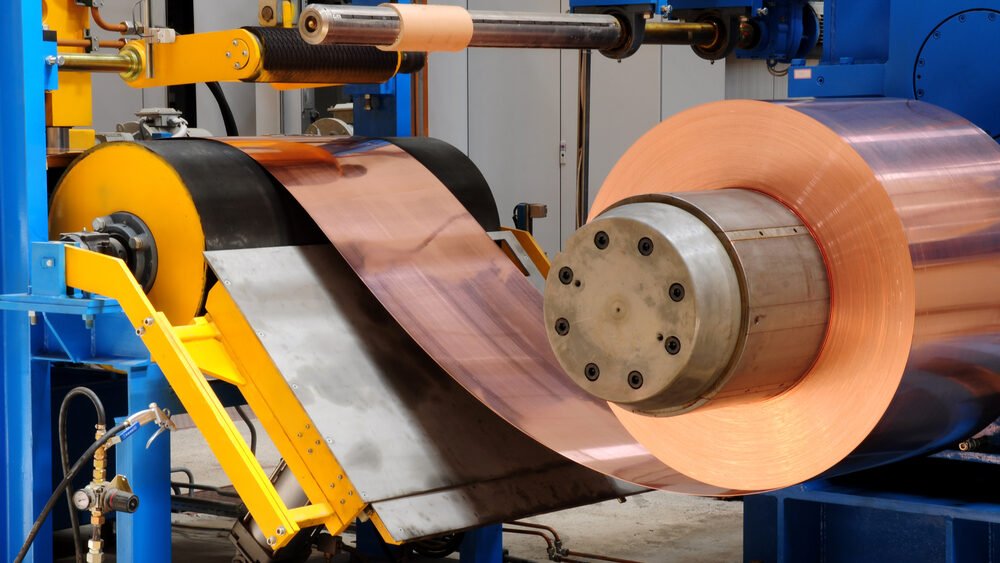
Chapter Six: How Bronze & Brass Are Made
Bronze was first made by our stone-age ancestors. It’s discovery, like many other discoveries, was likely accidental. People in Neolithic times searched for stones that were suitable for making tools. Imagine finding a shiny stone that, when pounded, didn’t crack like most stones—it dented! You can imagine how this would spark someone’s curiosity. Later, they saw that sufficient pounding could shape this shiny rock. Maybe they pounded it until it took the form of a knife or an arrowhead. Of course, we can never know for certain. What we do know is that this rock was native copper.
As time passed, they learned to melt this metal. They learned it could be poured into a mold in this melted state, allowing them to make a variety of shapes. Later, another happy accident occurred when native tin was added to the molten copper and bronze was born!
These actions mark the rudimentary beginnings of the science of metallurgy.
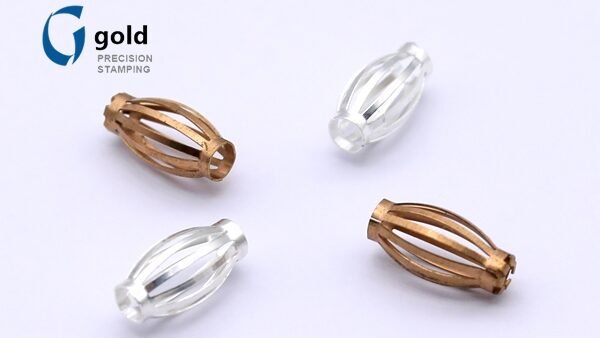
Making Bronze
Manufacturing bronze is not a complicated process. Copper and tin are melted together in various proportions and the result is bronze. It is isolating these elements from their ores that is problematic. Copper and tin are very rare in the native state. However, they exist in relative abundance in combination with other elements, which we call compounds.
Retrieving copper and tin from their respective ores is a process known as smelting. There are over 600 copper ores, with the top three being chalcopyrite (CuFeS2), chalcocite (Cu2S), and Covellite (CuS). As the formula shows, these are sulfites of copper.
Because chalcopyrite is the most common copper ore, we will use it as an example for the process.
First, the ore is reduced to copper sulfide, then calcium carbonate is added to form the slag. Next, with the addition of silica, the iron is removed as iron silicate slag, and last, the sulfur is removed by turning it into sulfur dioxide. What remains is almost pure copper.
Tin is almost never found in its native state and must also be extracted from ore, which is principally cassiterite (SnO2). The tin is extracted from the ore by roasting it with carbon at a temperature of 1371° Centigrade.
The reaction is:
SnO2+2C→Sn+2COSnO2+2C→Sn+2CO
The next step is leaching, which is done by adding acid or water solutions to remove any remaining impurities.
Once the copper and tin have been recovered from the ore, it is simply a matter of melting the two metals together in the desired proportions. It can then be poured into slabs, rolled, cold-rolled, extruded, etc.

Making Brass
Brass is an alloy of copper and zinc. As with bronze, creating brass is a simple matter of melting these two metals together in the desired proportions.
Complexities occur in deriving these metals from their respective ores. Earlier we addressed the process of extracting copper from its ore, and the process is no different when making brass.
Zinc is most commonly found in an ore known as zinc blende (ZnS). To liberate the zinc, the ore is roasted, forming zinc oxide (ZnO). Then the zinc oxide is mixed with coke (a grey, porous, hard fuel made by heating coal or oil in the absence of oxygen) in a 1 to 2 ratio, and heated to high temperatures. This reduces the ZnO to zinc. The formula describing the reaction is:
2ZnO+C→2Zn+CO2↑
Having recovered the copper and zinc from its respective ores, the two metals are melted together in the desired proportions. It can then be poured into slabs, rolled, cold-rolled extruded, etc.
In this chapter, you have learned how bronze and brass are made by extracting the needed metals from their ores, and you have learned the basics of extraction.
In the next chapter, you will learn the many uses of these metals.
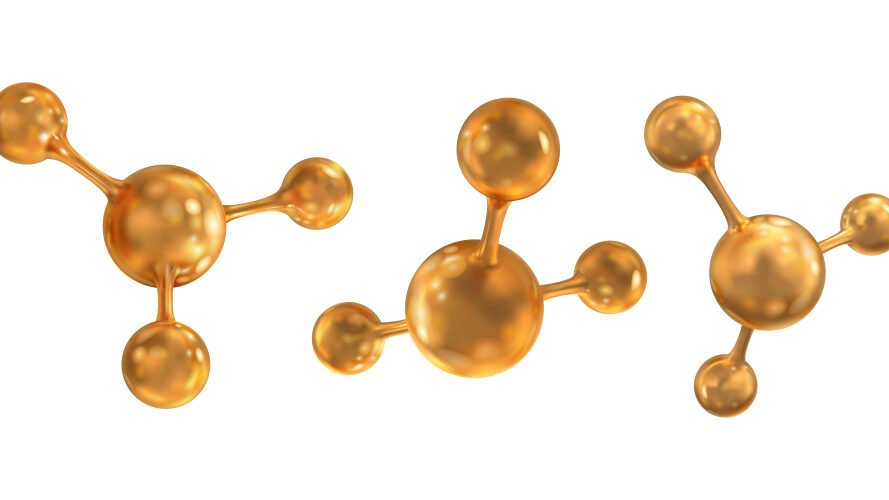
Chapter Seven: How Bronze & Brass Are Used
Bronze and brass have a multitude of uses, and the similarity between these alloys can cause overlapping uses. In other words, for certain uses, bronze and brass are equally acceptable metals. Therefore, you will see some degree of overlap.
Bronze—Common Uses
Bronze is used frequently in architectural applications such as
- Stair railings
- Window frames
- Mailboxes
- Interior and exterior cladding
- Furniture trim
Bronze is widely used in industrial applications, such as
- Bearings
- Pumps
- Bushings
- Valve stems
- Automobile transmission pilot bearings
- Electric motors
- Engine parts
- Hammers, mallets and wrenches (especially where sparking must be avoided)
- Springs
- Screws
Bronze is also used in the electrical and electronics industries for
- Electrical Contacts
- Electrical connectors
- Wire
Other examples include
- Bells
- Bronze wool (as opposed to steel wool)
- Coinage
- Medals
- Metal Clips
- Guitar and piano strings
- Mirrors
- Sculptures
Bronze is used in the music industry to make
- Cymbals
- Some saxophones
Bronze is used in maritime applications for
- Ship’s hulls
- Pumps
- Engine parts
- Propellers
Bronze is also used to make many components used in oil rigs. In short, this versatile alloy is found practically everywhere!
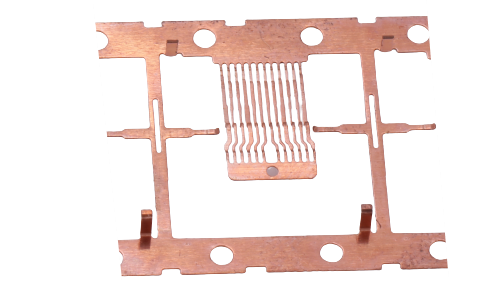
Brass—Common Uses
Brass has unique properties which make it one of the go to alloys for many manufacturers and products. As with bronze, there are many variations in brass. Basic brass is 67 percent copper and 33 percent zinc, however, the percentage of copper may range from 55 to 95 percent, and the zinc content can range from 5 to 45 percent.
While all brasses are ductile, versions with low zinc content are more ductile than those having a higher zinc content. Brass alloys are known for their machinability and will keep their strength after forming. This is of particular importance to the stamping industry.
The decorative use of brass is extremely common. Its color can range from light gold to almost red, making it well suited for
- Lamps
- Fittings
- Door Handles
- Pulls
Its anti-microbial properties are well documented, and it is often used for handles, railings, and other surfaces that receive significant public contact.
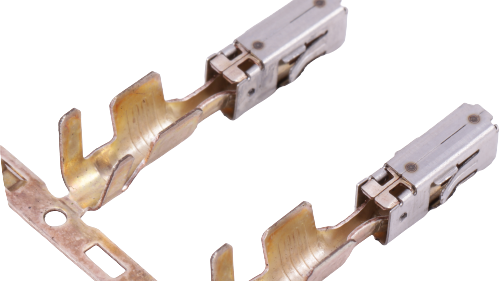
Brass has a low friction coefficient and is resistant to corrosion, making it ideal for
- Fasteners
- Connectors
- Tools
- Appliance parts
- Ammunition
- Bearings
- Gears
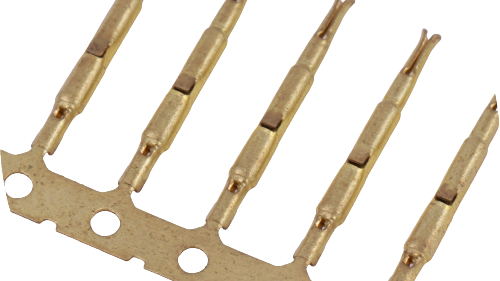
Brass offers excellent properties for making musical instruments such as
- Trumpets
- French horns
- Tubas
- Trombones
- Cornets
- Euphoniums
- Sousaphones
- Bells
Impressive though this list may be, it only scratches the surface.
In this chapter, you learned the many uses of bronze and brass in our daily lives. In chapter eight, the final chapter, I will ask you to draw on what you learned in chapters three, four, and five to help you decide which copper alloys should be chosen for particular tasks.
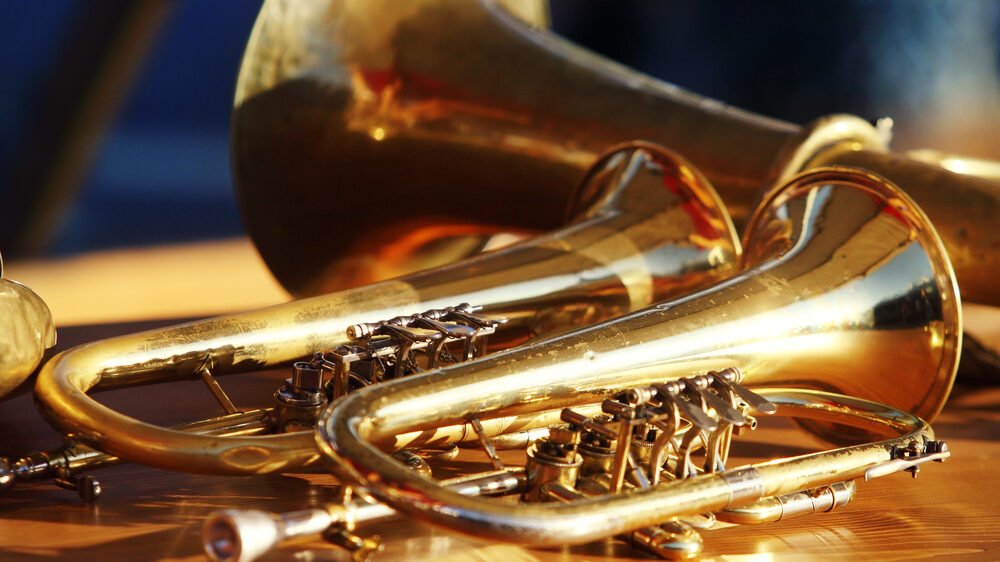
Chapter Eight: How to Choose the Right Copper Alloy for Your Purpose
I am often asked, “Should I choose bronze or brass?” In this chapter, I will answer that question.
Unfortunately, there isn’t just one answer. The choice depends upon the application, on the environment, and on other key factors.
Bronze and brass are widely used in a variety of industries, variables in strength, corrosion resistance, etc. make it understandable that choosing a bronze or a brass can be a tough proposition.
However, the diversity of available bronzes and brasses ensures your objectives are met and that everything will proceed as expected. Choosing correctly is just a matter of understanding your needs. In this chapter, we discuss the common needs that must be satisfied by making the correct choice.
Common Needs and the Copper Alloy that Meet Them
- The Amount and Type of Corrosion Resistance Desired
Many bronzes and brasses are chosen for their ability to resist corrosion.
Consider the type and amount of corrosion resistance required. Bronze and brass have different corrosion resistant profiles, with bronze usually coming out on top.
If cost is a factor (and when is it not), you can compromise with a less expensive brass alloy. However, most brasses offer lower levels of corrosion resistance in most environments than does bronze.
If stress and corrosion resistance parameters cannot be met by a bronze or brass alloy, you may need another alloy.
- Operating Environment
To what environment will the bronze or brass be exposed? This factor must be determined for you to make a good choice. Consider the environment in which your final product is used. For example, if you are changing out door hardware in a hospital, brass, because of its anti-microbial properties, would be a better choice than bronze.
Remember, not all types of bronze and brass can be welded. Take the steps necessary to find the appropriate brass or bronze for the job. Use what you have learned here to make the correct choice
- Mechanical Qualities
Toughness, yield strength, and ductility are crucial examples of the mechanical qualities you need to consider. In bronze and brass alloys, nickel produces toughness, and corrosion resistance.
Annealing, hot rolling and cold rolling can bronze and brass hardness, as can bending, swaging, and drawing, all at temperatures less than the temperature of recrystallization.
It should also be noted that although cold processes improve hardness, they will reduce other characteristics, such as impact resistance and elongation.
- The Magnetic Response (Permeability)
Brass and bronze are non-magnetic.
Because there are so many grades to choose from, you must decide which grade meets the demands of your application. By choosing the appropriate series and grade, you will complete your project successfully and save money.
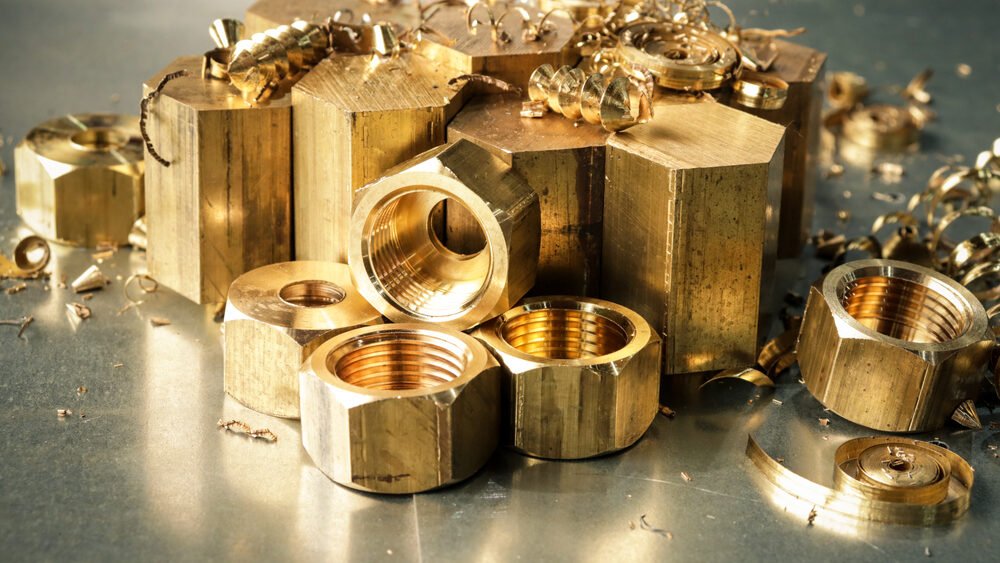
Conclusion
As you’ve learned, bronze and brass offer many well-known benefits plus a few unique ones that are not widely known. We learned that bronze and brass provide long service life, endure toxic environments, and resist corrosion better than steel.
Wear resistance depends on the grade. Abnormal ambient conditions, such as high salinity, can affect the service life of bronze and brass.
So, bronze and brass, ancient metals, while not perfect for every task, remain capable of meeting the challenges modern civilization puts to them.
The data within this guide is indicative only and should not be considered a substitute for the full specifications regarding these classes and grades. Notably, the parameters for mechanical properties can vary widely. The information within is based on current knowledge and is provided in good faith, but must not be regarded as a substitute for your own due diligence.
It may be useful at this point to recap key comparisons between bronze and brass so that you have the proper perspective on these metals.
- Bronze is a harder metal than brass and brittle by comparison. Brass is more malleable.
- Bronze has a melting point of 950 Celsius, while brass melts at 900 Celsius.
- Bronze offers excellent corrosion resistance, including saltwater. While brass offers a level of corrosion resistance, it falls short of bronze in this category.
- While bronze is suitable for decorative uses, brass is superior.
- Bronze is a much older metal in terms of the human experience when compared to brass, which was discovered some 3000 years later.
I hope you find this guide useful, and please, feel free to share it with your friends.