The intricacies of selecting materials for automotive wire terminals extend beyond mere conductive efficacy. It’s a meticulous balancing act, where material choices impact vehicle performance, safety, and align with evolving industry trends. This article delves into the critical considerations underpinning material selection for automotive wire terminals and explores how they influence modern vehicular innovations.
The selection of materials for automotive wire terminals is pivotal, encompassing considerations like conductivity, durability, corrosion resistance, and compatibility with automotive industry trends such as the surge in electric vehicles. The material choice directly correlates with vehicle performance, safety, and adherence to international standards, while also being swayed by consumer awareness and cross-industry innovations.
Venture with us as we unravel the nuances of material selection for automotive wire terminals, its implications on the automotive industry, and how it’s being shaped by external factors ranging from consumer demands to aerospace innovations.

What are the Critical Considerations when Choosing Materials for Automotive Wire Terminals?
Selecting the right materials for automotive wire terminals is a nuanced task that requires a thorough understanding of the operational demands and the environments in which these terminals will function. The chosen materials must align with the broader objectives of safety, performance, and cost-effectiveness. Here are the critical considerations that come into play:
- Conductivity:
- Electrical conductivity is paramount as it directly impacts the efficiency of power transmission within the vehicle’s electrical system. Materials with high conductivity ensure minimal energy loss, which is crucial for the overall performance, especially in electric and hybrid vehicles where energy efficiency is a priority.
- Durability:
- The automotive environment is demanding, with wire terminals being exposed to vibrations, thermal cycling, and mechanical stresses. Materials chosen should exhibit high durability to withstand these conditions over the vehicle’s lifetime. This durability extends to resistance against wear and tear during installation and maintenance.
- Corrosion Resistance:
- In the demanding world of automotive design, terminals are constantly battling against the relentless onslaught of moisture, salts, and other corrosive agents. This struggle is particularly intense in the harsh environments under the hood and along the chassis. To ensure that these vital connections maintain their integrity over time, it’s crucial to employ materials that can defy corrosion. This not only guarantees consistent electrical performance but is also a cornerstone of long-term vehicle reliability and safety.
- Compatibility with Vehicle Systems:
- The materials should be compatible with other materials and chemicals they may come into contact with within the vehicle system. Incompatibility could lead to premature failure or other issues that might jeopardize the vehicle’s performance or safety.
- Cost-effectiveness:
- While it’s important to prioritize performance and safety, cost-effectiveness remains a crucial consideration. The materials chosen should align with the budget constraints without compromising on the essential attributes. This also includes considering the cost of processing and assembling the terminals in addition to the raw material cost.
- Environmental Considerations:
- With a growing emphasis on sustainability, materials that are environmentally friendly or can be recycled are gaining traction. This is also in line with the global move towards more eco-friendly automotive solutions.
- Regulatory Compliance:
- Compliance with international and regional standards is crucial. Materials need to adhere to the regulations governing automotive components to ensure safety and quality.
- Ease of Processing:
- Materials that allow for easy processing, crimping, and connection are preferred as they contribute to efficient manufacturing and assembly processes, ultimately influencing the cost and quality of the automotive wire terminals.
- Thermal Properties:
- Given the varying temperatures within automotive environments, materials with stable thermal properties that can maintain their performance across a wide temperature range are desirable.
- Innovative Material Technologies:
- As we stride further into an era brimming with technological advancements, the emergence of new materials boasting superior characteristics opens up a realm of possibilities. These cutting-edge materials are not just a step forward in performance; they also offer a tantalizing competitive advantage in terms of cost-efficiency. For industries looking to stay ahead in the game, integrating these innovative materials could be a game-changing strategy.
In conclusion, choosing the right materials for automotive wire terminals is a complex yet crucial decision. It goes beyond just ensuring the electrical system works efficiently; it’s about enhancing the vehicle’s overall performance, safety, and cost-efficiency. Every factor plays a vital role, as these terminals must meet the rigorous demands of today’s advanced automotive systems. This decision, therefore, is not just a technical choice, but a strategic one that influences the vehicle’s quality and performance at every level.

Why is the Selection of Appropriate Materials in Automotive Wire Terminals Crucial for Vehicle Performance and Safety?
The materials chosen for automotive wire terminals play a decisive role in ensuring not only the operational efficiency but also the safety and long-term reliability of a vehicle. Here’s a closer look at how the material selection correlates with these critical aspects:
Electrical Efficiency:
- Optimal Conductivity:
- The essence of electrical efficiency lies in the seamless transmission of electrical signals or power. Materials with high conductivity facilitate efficient electrical transmission with minimal losses, which is critical for the operation of various vehicle systems, from powering electric motors to ensuring accurate sensor readings.
- Reduced Resistance:
- Lower contact resistance, enabled by appropriate material selection, ensures that less energy is lost in the form of heat. This is particularly significant in electric and hybrid vehicles where energy efficiency directly influences the vehicle’s range and performance.
- Heat Dissipation:
- Materials that are capable of effectively dissipating heat contribute to maintaining optimal operating temperatures within the electrical system, thereby promoting electrical efficiency and preventing overheating issues.
Long-term Reliability:
- Corrosion Resistance:
- Automotive environments can be harsh with exposure to moisture, salt, and other corrosive elements. Materials resistant to corrosion ensure that the integrity and functionality of the wire terminals are maintained over time, thus contributing to long-term reliability.
- Mechanical Durability:
- The mechanical durability of wire terminals, determined by the material’s strength and toughness, is vital for withstanding the rigors of automotive operations including vibrations, mechanical stresses, and thermal cycling.
- Environmental Stability:
- Materials that remain stable and retain their properties across varying temperatures and environmental conditions contribute to the long-term reliability of the electrical connections and, by extension, the vehicle’s overall electrical system.
Safety Implications:
- Prevention of Electrical Failures:
- The right materials help in averting electrical failures that could result from corrosion, overheating, or inadequate conductivity, all of which can have serious safety implications.
- Fire Safety:
- Materials with high melting points and good flame retardancy characteristics are crucial for preventing fire hazards, especially in scenarios of electrical short circuits or overloads.
- Maintaining Electrical Integrity:
- The material selection plays a pivotal role in ensuring the electrical integrity of the automotive systems. A stable and reliable electrical connection prevents malfunctioning of critical safety systems like anti-lock braking systems (ABS) or airbag systems, thus playing a vital role in ensuring vehicle safety.
- Compliance with Safety Standards:
- Adherence to international and regional safety standards is imperative. The material selection for wire terminals needs to comply with these standards to ensure the safety of the vehicle and its occupants.
In conclusion, the selection of appropriate materials for automotive wire terminals is a nuanced decision with far-reaching implications on the vehicle’s performance, safety, and long-term reliability. It’s a meticulous balance that underpins the operational efficacy and safety assurances of modern vehicles, underscoring the importance of informed material selection in automotive wire terminal design and utilization.

How are Automotive Industry Trends, like the Rise of Electric Vehicles, Impacting the Selection of Wire Terminal Materials?
The automotive industry is in a state of flux, with electric vehicles (EVs) at the heart of this transformation. This shift towards electrification is significantly impacting the selection of materials for wire terminals. Here’s how:
Adaptability to High-Voltage Systems:
- High Conductivity:
- Electric vehicles function using significantly higher voltages than those found in conventional vehicles with internal combustion engines. To ensure efficient power transfer within these high-voltage systems and to reduce energy loss, it’s crucial to use materials known for their superior electrical conductivity.
- Insulation and Dielectric Strength:
- With higher voltages come the necessity for better insulation and higher dielectric strength to prevent electrical breakdown and ensure safety. Material selections are leaning towards those that can provide robust insulation while maintaining excellent conductivity.
- Resistance to Arcing and Flashover:
- The materials need to resist electrical arcing and flashover, common challenges in high-voltage systems. This calls for materials that can withstand higher voltages without succumbing to electrical discharges.
Eco-friendliness:
- Recyclability:
- As the automotive industry moves towards more sustainable practices, the recyclability of materials used in wire terminals is gaining prominence. Materials that are recyclable or have a lower environmental impact are being favored.
- Reduced Hazardous Substances:
- The reduction or elimination of hazardous substances in wire terminal materials is another trend driven by both regulatory requirements and a growing emphasis on eco-friendliness.
- Life Cycle Analysis:
- The environmental impact of materials throughout their life cycle, from extraction to disposal, is being considered in the material selection process for automotive wire terminals, aligning with the broader industry trend of environmental responsibility.
Lightweighting:
- Material Minimization:
- The quest for lightweight vehicles to enhance fuel efficiency and reduce emissions is driving the selection of materials that can achieve the desired electrical and mechanical properties with minimal material usage.
- Utilization of Lightweight Materials:
- Materials such as aluminum and high-strength alloys that offer a good balance of weight and performance are gaining traction in the automotive wire terminal space. Lightweight materials contribute to the overall reduction in vehicle weight, which is critical for improving the energy efficiency of electric vehicles.
- Innovative Designs:
- Beyond just material selection, innovative designs that allow for the utilization of less material without compromising on performance are also part of the lightweighting trend.
Essentially, the emergence of electric vehicles and the overarching movement towards eco-friendliness and lightweight designs in the automotive sector are significantly influencing the choice of materials for wire terminals. These developments necessitate not only a re-evaluation but, in certain instances, a complete re-engineering of wire terminal materials to meet the advanced requirements of contemporary automotive systems. Viewed through this perspective, selecting materials for automotive wire terminals transcends a mere technical choice; it becomes a strategic decision that aligns with the wider trends and future directions of the automotive industry.

Why Might There be Resistance within the Automotive Industry to Adopt New Materials or Technologies for Wire Terminals, Despite Evident Benefits?
The automotive industry, given its long-established practices and the critical importance of safety and reliability, often exhibits a cautious approach towards adopting new materials or technologies. Here are some factors that contribute to this resistance, even in the face of evident benefits:
Initial Cost Implications:
- Investment in New Technologies:
- Adopting new materials or technologies often entails significant initial investments in research, development, and equipment. The financial outlay required for exploring and incorporating novel materials or technologies can be a deterrent.
- Cost of Certification:
- To meet automotive industry standards, new materials and technologies are subject to extensive testing and certification. This process, often lengthy and expensive, can pose significant barriers for many industry participants.
- Price Sensitivity:
- The automotive sector is highly price-sensitive, with fierce competition driving a relentless focus on cost control. Any cost increase, even if it’s an investment in superior materials or technologies, is scrutinized against the backdrop of market competitiveness and profitability.
Lack of Established Standards or Familiarity:
- Inadequate Standardization:
- The lack of established standards for new materials or technologies can create uncertainty. The industry relies on well-defined standards to ensure quality, safety, and interoperability, which might not yet exist for new and unproven materials.
- Familiarity and Proven Track Records:
- Manufacturers, suppliers, and other stakeholders have familiarity and comfort with existing materials and technologies which have proven track records. New materials or technologies pose unknown risks and may require new knowledge and skills which can be seen as disruptive.
- Supply Chain Adjustments:
- New materials may necessitate adjustments in the supply chain, including sourcing from new suppliers or adapting manufacturing processes. These changes can be complex and challenging to implement, particularly in the tightly integrated automotive supply chains.
Resistance to Change:
- Inertia:
- Organizational inertia and a preference for maintaining the status quo can be significant barriers to adopting new materials or technologies. The “if it’s not broken, don’t fix it” mentality can prevail, especially in an industry with deeply ingrained practices.
- Perceived Risks:
- The perceived risks associated with the adoption of new materials or technologies, both in terms of performance and financial outlay, can outweigh the perceived benefits, leading to resistance.
- Lack of Urgency or Incentives:
- Unless there is a compelling regulatory or market-driven incentive, the motivation to adopt new materials or technologies may be lacking.
In conclusion, the resistance to adopting new materials or technologies for wire terminals in the automotive industry is a multifaceted issue. It’s intertwined with financial considerations, standardization and familiarity concerns, and a general resistance to change rooted in the industry’s inherent caution and the high stakes involved in automotive manufacturing and safety. Overcoming these barriers requires a concerted effort from stakeholders across the automotive ecosystem, including manufacturers, suppliers, regulatory bodies, and the end consumers, who ultimately drive demand for more advanced, efficient, and sustainable automotive solutions.

Who Sets the International Standards for Wire Terminal Materials, and How Do They Influence Manufacturing Decisions?
Navigating the landscape of automotive manufacturing necessitates adherence to a myriad of standards, ensuring not only the quality and safety of products but also their compatibility and interoperability across global markets. Here’s a brief look at the bodies that set international standards for wire terminal materials and the impact of these standards on manufacturing decisions:
Overview of International Standards:
- International Organization for Standardization (ISO):
- ISO is a global entity that develops and publishes international standards, including those pertinent to automotive wire terminal materials. Standards like ISO 6722 and ISO 14572 are examples that pertain to automotive wires and their performance requirements.
- Society of Automotive Engineers (SAE):
- SAE International is a professional association and standards organization that delineates standards for various automotive components, including wire terminals. SAE J1128 is an example of a standard that specifies the performance requirements of electrical cables used in road vehicles.
- International Electrotechnical Commission (IEC):
- IEC is another global standards organization that sets standards for electrical and electronic technologies, which include wire terminal materials for automotive applications.
- Underwriters Laboratories (UL):
- UL is a nonprofit organization that develops standards for products’ safety, including electrical components like automotive wire terminals.
- Automotive OEM Standards:
- Besides global and regional standards organizations, individual automotive original equipment manufacturers (OEMs) often have their own stringent standards and specifications that suppliers must adhere to.
Influence on Material Selection and Manufacturing:
- Quality Assurance:
- Adhering to internationally recognized standards ensures a level of quality and reliability in wire terminal materials, which is crucial for maintaining the integrity of electrical systems in vehicles.
- Market Access:
- Compliance with international and regional standards is often a prerequisite for accessing markets. Manufacturers who adhere to these standards can sell their products globally, while non-compliance can result in restricted market access.
- Reduced Liability:
- Standards compliance reduces the risk of product liability claims. It demonstrates that a manufacturer has followed internationally recognized best practices in material selection and manufacturing processes.
- Supply Chain Consistency:
- Standards provide a common language and set of expectations that streamline interactions and transactions along the supply chain, facilitating consistency in material specifications and quality.
- Innovation and Continuous Improvement:
- The process of adhering to, or exceeding, standards can drive innovation and continuous improvement in material selection and manufacturing processes, pushing the industry forward.
- Consumer Confidence:
- Standards also play a role in building consumer confidence. Knowing that products meet internationally recognized standards for safety and quality can be a significant selling point.
- Regulatory Compliance:
- International standards often form the basis for regulatory compliance, making adherence to these standards a legal obligation as well as a best practice.
In conclusion, the international standards for wire terminal materials are not just technical benchmarks but pivotal frameworks that shape manufacturing decisions, market access, and the overall trajectory of innovation and quality assurance in the automotive industry. They play a crucial role in aligning the industry towards common goals of safety, efficiency, and interoperability, thereby facilitating a global automotive ecosystem that thrives on shared principles and continuously evolving standards of excellence.

What Role Does Consumer Awareness and Demand Play in Driving Innovation in Wire Terminal Materials?
The automotive industry, like any other, is fundamentally driven by the needs and demands of its consumers. In a domain as technical as automotive wire terminals, one might overlook the influence of consumer awareness and demand, yet they play a pivotal role in driving innovation in wire terminal materials. Here’s how:
Impact of Consumer Preferences:
- Safety Concerns:
- Consumers are increasingly aware of the safety aspects of vehicles, including their electrical systems. Any incidence of electrical failures or fires can significantly tarnish a brand’s reputation. This consumer sensitivity towards safety drives manufacturers to innovate in wire terminal materials to ensure robust, fail-safe electrical connections.
- Environmental Awareness:
- The growing environmental consciousness among consumers is pushing the automotive industry towards more sustainable practices. This includes the use of eco-friendly materials in wire terminals, which can reduce the environmental impact throughout the vehicle’s lifecycle.
- Fuel Efficiency and Performance:
- Consumers demand vehicles that are fuel-efficient, and electrically efficient wire terminals contribute to this goal by minimizing electrical losses. Furthermore, the performance aspect, especially in high-performance and electric vehicles, necessitates the use of materials that can withstand high temperatures and harsh conditions, driving innovation in wire terminal materials.
Demand-Driven Innovations:
- Lightweighting:
- The quest for fuel efficiency has propelled the trend of lightweighting in the automotive industry. Consumer demand for more fuel-efficient vehicles drives innovation in lightweight materials for wire terminals, contributing to the overall reduction in vehicle weight.
- Cost-Effectiveness:
- Despite the desire for enhanced features, consumers are price-sensitive, pushing manufacturers to innovate in cost-effective materials that do not compromise on quality and performance.
- Longevity and Durability:
- Consumers expect durable vehicles that require minimal maintenance. The demand for longevity drives manufacturers to explore materials for wire terminals that can withstand the test of time and harsh operating conditions.
- Integration of Advanced Technologies:
- As vehicles become more sophisticated with integrated advanced technologies, the demand for compatible and high-performance wire terminal materials grows. Consumers’ appetites for technologically advanced vehicles drive the need for innovative materials that can meet the electrical and mechanical demands of modern automotive systems.
- Customization and Specialty Vehicles:
- The growing market for customized and specialty vehicles also drives innovation in wire terminal materials to meet specific consumer demands and unique application requirements.
In conclusion, the evolving consumer awareness and demand are integral drivers of innovation in wire terminal materials. They push the boundaries of what’s possible, encouraging manufacturers to explore new materials and technologies that can meet and exceed consumer expectations. This symbiotic relationship between consumer demand and industry innovation is what propels the automotive industry forward, ensuring it remains responsive, relevant, and competitive in a rapidly changing world.

How are Innovations in Other Industries, like Aerospace or Electronics, Influencing Advancements in Automotive Wire Terminal Materials?
The automotive industry doesn’t operate in a vacuum; it’s significantly influenced by advancements in adjacent industries like aerospace and electronics. The cross-pollination of ideas and material innovations between these domains often leads to the evolution of automotive wire terminal materials. Here’s a dive into how this cross-industry influence manifests:
Cross-Industry Material Innovations:
- Lightweight and High-Strength Materials:
- The aerospace sector is renowned for its reliance on lightweight yet robust materials, such as titanium and advanced composites, to fulfill strict requirements regarding weight and performance. Similarly, the automotive industry, driven by its quest for fuel efficiency and enhanced performance, frequently adopts comparable materials for wire terminals. This approach aims to reduce weight while simultaneously preserving or even improving durability and performance.
- High-Temperature Resistant Materials:
- Both aerospace and electronics industries deal with high-temperature environments, pushing the envelope in developing materials that can withstand extreme temperatures. These material innovations find their way into the automotive industry, enhancing the performance of wire terminals in high-temperature automotive applications.
- Corrosion-Resistant Materials:
- Aerospace, with its exposure to harsh environmental conditions, has led the charge in developing corrosion-resistant materials. These materials are increasingly adopted in automotive wire terminals to enhance longevity and reliability.
- Advanced Conductive Materials:
- The electronics industry is at the forefront of developing materials with superior electrical conductivity. The adoption of such materials in automotive wire terminals can significantly reduce electrical resistance, improving energy efficiency and system performance.
Adoption of Aerospace or Electronic Material Standards:
- Material Quality Standards:
- The stringent quality standards often associated with aerospace and electronics materials are gradually being adopted by the automotive industry to ensure the reliability and safety of wire terminals.
- Miniaturization and Precision:
- The electronics industry’s focus on miniaturization and precision has a ripple effect on the automotive industry, pushing for more compact, precise wire terminal designs that can handle complex, high-density electrical systems.
- Material Processing Technologies:
- The automotive sector is increasingly adopting advanced material processing technologies, originally developed in the aerospace and electronics industries. Techniques like additive manufacturing and high-precision stamping are now being utilized to enhance the quality and performance of wire terminals.
- Electromagnetic Interference (EMI) Shielding:
- With the increase in electronic systems in vehicles, EMI shielding, a concept well-established in the electronics industry, is becoming crucial in automotive wire terminal materials to prevent interference and ensure reliable operation of electronic systems.
- Material Testing and Certification Protocols:
- The rigorous testing and certification protocols employed in aerospace and electronics are influencing the automotive industry’s approach to validating the performance and safety of wire terminal materials.
In conclusion, the symbiotic relationship between the automotive, aerospace, and electronics industries accelerates the pace of innovation in wire terminal materials. By adopting and adapting material innovations and standards from these adjacent industries, the automotive sector continues to enhance the performance, safety, and reliability of wire terminals, aligning with the evolving demands of modern vehicles and the expectations of an increasingly informed and discerning consumer base.
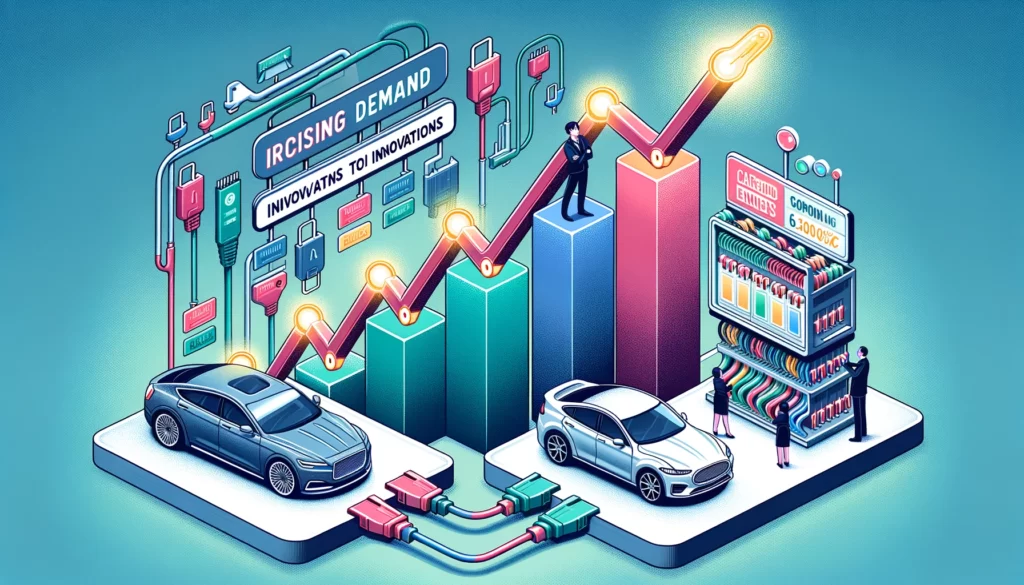
Conclusion
The selection of materials for automotive wire terminals is a crucial aspect that significantly impacts vehicle performance, safety, and sustainability. This meticulous selection is driven by various factors including inherent material properties, industry standards, consumer demands, and innovations from adjacent industries like aerospace and electronics.
Key takeaways from the discussion include:
- Material Properties: Conductivity, durability, and corrosion resistance are fundamental considerations ensuring the effectiveness and longevity of wire terminals.
- Industry Trends: The rise of electric vehicles is pushing for materials that can adapt to high-voltage systems, emphasizing lightweight and eco-friendly solutions.
- Cross-Industry Innovations: Advancements in aerospace and electronics are influencing the automotive industry by introducing high-strength, temperature-resistant, and corrosion-resistant materials alongside new processing technologies.
- Consumer Demand: Evolving consumer awareness and preferences are driving demand for safer, more efficient, and environmentally sustainable material choices.
The evolving landscape of material selection for automotive wire terminals symbolizes the broader aspiration of the automotive industry to innovate, enhance performance, and meet the rising standards of safety and environmental responsibility.