Everything You Need to Know from Discovery to History to Contemporary Uses
By
Jony Chen
Copyright
Thee Ultimate Guide to Stainless Steel, Copyright © 2022 by Jony Chen. All rights reserved. No part of this book may be reproduced or used in any form or by any means, electronic or mechanical, including photocopying, or recording, or by any information storage or retrieval systems, without permission in writing from the author or the publisher.
Legal Notice
Under no circumstances will I hold any blame or legal responsibility against the publisher, or the author, for any damages, reparations, or monetary losses for the information contained within this book, either directly or indirectly.
Disclaimer
Please note that the information contained within this document is for educational and entertainment purposes only. We have tried to present accurate, up-to-date, reliable, and complete information. No warranties, express or implied, are made by the author or the publisher. Readers acknowledge the author is not engaged in rendering legal, financial, medical or professional advice.
Introduction
This book provides the reader not only a broad overview but also a working knowledge of stainless steels. You have questions! Such as—What advantages do stainless steels offer? What is stainless steel and how does it differ from other steels? How can I decide which stainless steel is the right choice for my purposes?
The answers to these questions and many others are provided in the pages that follow. For example, the element chromium is primarily responsible for stainless steel’s resistance to rusting.
In this era of credibility crisis, trust needs to be earned. Readers should be confident that I have expertise in this subject, having co-founded Gold Precision Co. Ltd. in 2012. Gold Precision is a metal stamping manufacturer that serves customer needs from prototyping to the final product, including stamping mold design, mold trial, processing and assembly.
This guide will allow you to make informed decisions regarding the products you buy, the material you use to manufacture your products, the material’s properties (including pros & cons), and other valuable insights.
The information in this guide will save you from making costly mistakes, so the sooner you read it, the better.

Chapter One: Stainless Steel—an Introduction and Brief History
Imagine a world without stainless steel. Tableware, cutlery, appliances, and so many other items we take for granted, would have a decidedly shorter life span because of rust and corrosion. Fortunately, this world exists only in our imagination since the development of stainless steel.
Stainless steel is defined as an alloy, principally composed of iron, combined with around 11 percent chromium, which gives stainless steel the bulk of its anti-corrosive properties.
A Short History
One might reasonably credit French chemist Louis Vauquelin with the first step toward stainless steels as he discovered chromium in 1797 at just 24 years of age. It wasn’t until the early 1800 that such notables as Michael Faraday, Robert Mallet, and James Stoddard took notice of the corrosion resistance offered by iron-chromium alloys. By 1821, Pierre Berthier recognized the potential of stainless steel for cutlery because it did not rust and was unaffected by acids.
German steelmaker Krupp AG, founded in 1811, produced steel through the waning days of the 20th century, merging with Thyssen AG in 1999 to become ThyssenKrupp AG in 1999. It was Krupp who began manufacturing chromium steel in the 1840s and by the 1850s, this steel was being used in cannon manufacturing. Englishman Benjamin Huntsman founded Sheffield Steel Works in 1771 and his company also produced chromium steel cannon in the 1850s. The company is now owned by the UK’s Ministry of Defense.
Strangely, no one ever applied for a patent until another Englishman, Robert Forester Mushet, applied for and received a patent in 1861. A patent was not issued in the U.S. until 1869. The first major construction project using a chromium steel was the Brooklyn bridge, completed in 1883, taking 14 years to complete.
The late 1890s saw a breakthrough in isolating carbon-free chromium. Hans Goldschmidt, a German chemist, improved an aluminothermic reduction for making carbon free chromium, making it more accessible as an alloy for stainless steel, which led researchers to develop many of the alloys we use today.
By 1911, Phillip Monnartz had defined the relationship of chromium to corrosion resistant steel. In 1912, Krupp metallurgists Benno Strauss and Eduard Maurer had created austenitic stainless steel, naming it Nirosta.
Meanwhile, developments in the United States were taking place. Frederick Becket and Christian Dantsizen were manufacturing ferritic stainless steel, and in 1912, Elwood Haynes sought a US patent for a martensitic stainless steel alloy, which was finally awarded in 1919.
Across the pond, Harry Brearley of the Brown-Firth research laboratory in Sheffield, England, discovered a martensitic stainless steel alloy in 1912 for rifles.
Firth Vickers sold Brearley’s alloy under the Staybrite brand in England, and in 1929 it was used in the entry awning for London’s Savoy Hotel.
In 1915, Brearley sought a US patent but discovered that Elwood Haynes had already registered one, so Haynes and Brearley pooled their capital, founding the American Stainless Steel Corporation in Pittsburgh, Pennsylvania.
Within the metallurgy field, the name for this new alloy remained unsettled. In the U.S., it was sold under various brand names, including Nirosta and Alleghany metal. Unstainable steel was coined by a trade journal in 1921, which later morphed into stainless steel. Prior to the Great Depression, over twenty-five thousand tons had been produced and sold annually in the U.S.
Continued technological progress throughout the 1950s and 1960s allowed increased production at a low cost. Advances included:
- Argon oxygen decarburization (AOD) which removed sulfur and carbon
- Continuous casting and hot strip rolling
- The Sendzimir cold rolling mill, often referred to as the Z-Mill
Current Uses
Stainless steels have a wide range of applications, including appliances, wedding rings and everything in between. This versatility is possible because stainless steel can be formed into tubing, wire, sheets, bars, and plates. With these options, manufactures can readily produce cookware, cutlery, storage tanks, surgical instruments, and various industrial equipment. Today, its corrosion and chemical resistant properties are exploited in countless ways.
Stainless steel has a rich history that spans four centuries. In the next chapter, you will learn about the five types of stainless steel and their corresponding grades.

Chapter Two: Classes and Grades
Now that you have a bit of history, I hope I’ve piqued your curiosity sufficiently to appreciate the deeper details regarding stainless steel.
As the chapter title suggests, we will dive into the five classes of stainless steel, followed by some in-depth information on the various grades of stainless steel represented within them.
Classes of Stainless Steel
I should point out that these five classes are the predominant ones, but there are other exotic stainless steel alloys out there, in fact, over 100! This diversity directly results from the many roles stainless steel has been called upon to fulfil. Beyond chromium, steel is alloyed with nickel, manganese, silicon, nitrogen, and, of course, carbon to achieve the properties required for a given application. These applications may require strength, flexibility, heat resistance, ductility, or some combination of these properties.
The five predominant classes/families of stainless steel we focus on in this guide are defined by their crystalline structures. They are Austenitic, Ferritic, Martensitic, Precipitation hardened, and Duplex stainless steels.
Austenitic Stainless Steel
lel producedirds of all the stainless steelthat we focus od chromium, steel is alloyed with nickel, Of the predominant five, Austenitic stainless steel is the most common, comprising roughly two-thirds of all the of all stainless steel produced. An austenitic microstructure is a cubic face-centered crystalline design, achieved by alloying steel with nitrogen, manganese, and nickel to create the austenitic microstructure. Since austenitic stainless steels maintain their microstructure through all temperatures, they are not hardened at any point in the manufacturing process.
Austenitic stainless steels can be further divided into two main sub-classes, the 200 series and the 300 series.
The 200 series nickel-manganese-chromium alloys also use nitrogen and manganese to reduce the use the amount of nickel and increase its strength to around 50 percent higher than 300 series stainless steel plates.
- Type 201 is can be hardened by cold working.
- Type 202 has general purpose uses. However, the reduced nickel content means 202 loses much of its resistance to corrosion.
- The 300 series is a nickel-chromium alloy that reaches its austenitic microstructure only by nickel alloying, although some grades contain nitrogen to decrease the need for nickel. The most widely used stainless steels are in the 300 series.
- Type 304: The best-known grade is Type 304, also recognized as 18/8 and 18/10, for its composition of 18 percent chromium and 8 or 10 percent nickel, respectively.
- Type 316: The next most known austenitic stainless steel is Type 316. The addition of 2 percent molybdenum offers improved acid and corrosion resistance owing to chloride ions. Minimal-carbon versions, such as 304L or 316L, have carbon ratios of 0.03 percent or less, and are used to resist corrosion problems created by welding.
Ferritic Stainless Steels
Ferritic stainless steels have a ferrite microstructure featuring a cubic face-centered crystal design much the same as carbon steel, which is composed of 10.5 to 27 percent chromium with little or no nickel. This microstructure exists through all temperatures because of the chromium, so it cannot be hardened by heat treatment, nor can it be hardened to the same degree as austenitic stainless steels. Ferric stainless steels are magnetic, unlike austenitic stainless steels.
Zirconium (Zr), titanium (Ti), and niobium (Nb) to Type 430 offer good weldability when added.
Ferric stainless steels are not as expensive as austenitic steels because of their low nickel content, which is one reason they are widely used. Examples include:
- Type 409Cb and 409 are used for automobile exhaust pipes in North America and in Europe… types 441 and 439 are in common use for this product
- Grade 430, which comprises 17 percent Cr, is frequently used in architectural applications
- Ferric steels are common building elements for chimney ducts, roofing, and slate hooks
- Solid oxide fuel cells contain power plates operating at temperatures about 1,292 °F (700 °C) which are made from high-chromium ferritic steel that are composed of 22 percent Cr
Martensitic Stainless Steels
Martensitic stainless steels have an extremely broad range of uses. They are used for stainless steel tools, in applications requiring creep-resistance, and in engineering applications. Creep resistance refers to an alloy’s tendency to deform over a long period of exposure to high stress levels. Unlike austenitic and ferritic stainless steel, martensitic stainless steels are magnetic, and they lack the corrosion resistance offered by austenitic and ferritic stainless steel because they contain low chromium content. There are four predominant types (with some overlap).
- Fe-Cr-C grades. These were the first grades to be used and they remain in broad use for their ability to resist wear. Martensitic stainless steels are used in engineering applications.
- Fe-Cr-Ni-C grades. Nickel content exceeds carbon content, which offers exceptional corrosion resistance and toughness. Type EN 1.4303 (CA6NM, the casting grade) has 4 percent Ni and 13 percent Cr. These grades are used for turbines in hydroelectric power plants because of its good casting characteristics, resistance to cavitation wear, and excellent weldability.
- Precipitation hardening types. Type EN 1.4542, also known as 17/4PH, is the most commonly used grade, merging precipitation hardening and martensitic hardening. It achieves high strength and is known for its overall toughness. For these reasons, it is widely used in the aerospace industry and others.
- Creep-resisting grades. Miniscule additions of cobalt, vanadium, niobium, and boron enhance creep resistance and strength up to 650 °C (1,202 °F).
Precipitation Hardened Stainless Steels
Precipitation hardened stainless steels exhibit anti-corrosion properties, much as do austenitic varieties. Precipitation hardened stainless steels can be rush hardened to higher strengths than some grades of martensitic, which gives such steels an advantage. There are three kinds of precipitation hardened stainless steels:
- Martensitic 17-4 PH[49] (AISI 630 EN 1.4542) contains about 17 percent Cr, 4 percent Ni, 4 percent Cu, and 0.3 percent Nb.
- Semi-austenitic 17-7PH[49] (AISI 631 EN 1.4568) contains about 17 percent Cr, 7.2 percent Ni, and 1.2 percent Al.
- Austenitic A286[50](ASTM 660 EN 1.4980) contains about Cr 15 percent, Ni 25 percent, Ti 2.1 percent, Mo 1.2 percent, V 1.3 percent, and B 0.005 percent.
Duplex Stainless Steels
Duplex stainless steels exhibit a compound microstructure, that of both ferrite and austenite, with the ideal being 50:50 ratios. However, commercial alloys may have 40:60 ratios.
This alloy includes up to 5 percent molybdenum, and chromium levels of 19 to 32 percent. Duplex stainless steels also have a lower nickel content than austenitic stainless steels, yet they have twice the strength of austenitic stainless steel.
Its mixed microstructure offers superior resistance to cracking and its properties limit chloride stress corrosion when compared to 304 and 316 austenitic stainless steel.
Duplex stainless steels are marked by three subgroups which reflect their corrosion resistance: 1) standard duplex, 2) super duplex, and 3) lean duplex.
The characteristics of duplex stainless steels are reached with a lower alloy content than high-performing austenitic grades, making them cost-effective and suitable for a variety of applications.
Duplex stainless steel is used heavily in the paper and pulp industry.
Currently, it is primarily used the oil and gas industries, which have urged development into more corrosion resistant capabilities, which has resulted in the super duplex and hyper duplex grades having enhanced corrosion resistant properties.
Less costly and fewer corrosion resistant duplex steels have been developed that are used in structural applications, such as concrete reinforcing bars, coastal works, bridge slabs, and the like.

Grades
Next, we will discuss the many stainless steel grades available. They include 100 through 900.
Type 100 Series
Type 102—an austenitic stainless steel for general purpose use.
Type 200 Series
Type 200—chromium-manganese-nickel alloys, which use manganese along with nitrogen to minimize the use of nickel. Nitrogen increases the yield strength, giving 200 series alloys around 50 percent greater yield strength than 300 series stainless steel. Yield strength is
Type 200 is one of the strongest stainless steels, exhibiting a low vapor pressure, low gas content, magnetic components, high electrical and thermal conductivity. Its chemical formulation makes the chromium-manganese-nickel alloy highly corrosion resistant to alkaline and salt solutions, as well as durable at temperatures below 600º Fahrenheit.
It has low corrosion rates in distilled and tepid water, and can be formed cold by all techniques and hot-formed to any profile.
Common uses of type 200 series alloys include:
- Salt production
- Equipment used in food processing
- Caustic environments
- Offshore and marine engineering
- Vessels and reactors in which fluorine is produced
- The manufacture or handling of sodium hydroxide, especially at temperatures exceeding 300° Fahrenheit
Type 300 Series
Type 300—stainless steel is categorized as austenitic, and cold-working techniques can only harden it. These stainless steel types contain 18 to 30 percent chromium and 6 to 20 percent nickel as significant elements in the alloy.
Type 304—is the most commonly used alloy among various kinds of stainless steel. Series 300 stainless steel alloy is corrosion resistant, sustains its strength at high temperatures, and are easy to maintain.
Grade 301—is extremely flexible, hardens quickly through mechanical working, and has better wear resistance, weldability, and fatigue strength than 304.
Grade 302—offers similar wear resistance as 304, but slightly higher in strength because of the additional carbon.
Grade 303—is a robust version of 304 because of the addition of phosphorus and sulfur, and is also known as A1 based on ISO 3506.
Grade 304—is the best known grade. It is classic stainless steel 18/8 (18 percent nickel—8 percent chromium). It is known outside the U.S. as A2 stainless steel, according to ISO 3506 (not to be confused with A2 tool steels). The Japanese equivalent for this material is SUS304.
Grade 304L—is similar to grade 304, but its carbon content has been reduced to enhance weldability, making it slightly weaker than 304.
Grade 304LN—is similar to 304L, but with added nitrogen for higher tensile and yield strength.
Grade 305—is much like 304, but with extra nickel to reduce work hardening.
Grade 308—is used when welding 304, as filler metal.
Grade 309—has superior resistance to temperature extremes than does 304, and is used as filler metal when welding various grades of steels, along with Inconel, which is an alloy of nickel containing chromium and iron.
Grade 310, 310S—is a stainless high-alloy austenitic steel used in high temperature environments. Its high chromium and nickel content provide excellent resistance to oxidation and great strength at high temperatures. It is ductile with good weldability, which allows it to be used in many applications.
Grade 316—is the second most common class (after 304) used for surgical instruments and in the food industry. The addition of molybdenum prevents specific forms of corrosion. It is also recognized as a marine grade stainless steel because of its resistance to chloride corrosion, and it is widely used in nuclear reprocessing plants.
Grade 316L—is a deficient carbon form of 316, used in stainless steel marine applications, dive watches, and the manufacture of nuclear reactor pressure containers because of its high corrosion resistance. It is also known as A4, according to ISO 3506.
Grade 316Ti—is a variant of grade 316, which incorporates titanium to increase heat resistance. It is used in elastic chimney liners.
Grade 321—is similar to 304 but less prone to weld decay because of the addition of titanium. See 347 with the addition of niobium for desensitization when welding.
Type 400 Series—The 400 series stainless steels contain 11 percent more chromium and are 1 percent higher in manganese content than the 300 series group. The 400 series is subject to rust and corrosion in some conditions. Heat treatment hardens the 400 chains. The 400 series stainless steel has a high carbon content, giving it a martensitic crystal structure, which offers high strength and elevated corrosion resistance. However, martensitic stainless steels are not as resistant to corrosion as the austenitic types.
Grade 405—is made from iron for welding applications.
Grade 408—is heat resistant with weak corrosion resistance (8 percent nickel—11% chrome).
Grade 409—is inexpensive and used for car exhausts.
Grade 410—is a martensite (high-strength chromium/iron). It is wear-resistant, but has a low resistance to corrosion.
Grade 416—is easy to machine because of its sulfur content.
Grade 420—is martensitic and widely used for silverware. It is similar to Brearley’s original stainless steel, and it boasts excellent polishing ability.
Grade 430—is largely decorative. It is a ferritic, has good formability, but low corrosion and temperature resistance.
Grade 439—is an iron grade, used in catalytic converters. Its increased chromium level improves temperature and corrosion resistance.
Grade 440—is used in high quality cutlery. Its extra carbon provides superior edge retention, and can be hardened to a Rockwell 58 rating, making it one of the hardest stainless steels available. Because of its toughness and relatively low price, most show, replica knives and swords are made of 440 stainless steel, which is available in four types:
Grade 440A—contains has the lowest carbon content, making it highly stain resistant.
Grade 440B—contains slightly levels of carbon than 440A.
Grade 440C—has a massive amount of carbon compared to the other 440 variants. It is the most popular variant for knife making, excluding diving or other saltwater applications. It is also more readily available than the other 440 options.
Type 440F—has the same elevated carbon content as 440C.
Grade 446—is used for or high-temperature service.
Type 500 Series—are heat resistant chromium alloys
Type 600 Series—are proprietary alloys and are not given SAE grade numbers. The 600 series stainless steel alloys find service in applications requiring high temperature and corrosion resistance. The 600 series alloys have excellent mechanical characteristics, providing a good workability and high strength, and its high nickel content offers fewer incidents of corrosion stress cracking when annealed.
601 through 604—are low-alloy martensitic steels.
610 through 613—are martensitic hardened secondary steels.
614 through 619—are chromium martensitic steels.
630 through 635—are stainless steels that harden by semi-austenitic and martensitic precipitation.
650 through 653—are hot / cold work strengthened austenitic steels.
660 through 665—are austenitic super alloys; All types except for alloy 661 are hardened by second stage precipitation.
Type 900 Series—are austenitic chromium-molybdenum alloys.
Type 904—is similar to 316 but with increased molybdenum and chromium content for greater corrosion resistance.

Chapter Three: Stainless Steel—Strengths, Mechanical and Other Properties
A stainless steel’s strength, mechanical, and other requirements are typically provided in the purchase order or request for proposal (RFP). These specifications apply to the finished product and its profile.
Meeting these specifications results in an appropriately manufactured product of high quality. Engineers handle the facilities and equipment in order to ensure that working pressures and loads meet all safety standards.
The mechanical characteristics of flat-rolled products ordinarily include yield stress (or proof stress), tensile strength, as measured by the Rockwell and Brinell tests for hardness. The characteristics needed for bar, tube, pipe, and fittings typically include yield stress and tensile strength.
Stainless Steel’s Mechanical Properties
- Yield Strength
Unlike mild steels, annealed austenitic stainless steel yield strengths are measured as a percentage of tensile strength. Mild steel yield strength is typically 65-70% of the tensile strength, while only 40 to 45 percent in the austenitic stainless family.
Cold working quickly and dramatically increases yield strength. For example, tempered spring wire can be cold worked to increase the yield strength to 80 to 95 percent of its tensile strength.
- Ductility
The inherent properties of cold work hardening and high ductility\elongation make stainless steel extremely easy to fabricate. These characteristics make stainless steel ideal for deep drawing.
Ductility is the amount of material will stretch before breaking. This is determined during tensile testing. Annealed austenitic stainless steels have extraordinarily high elongations, with results in the 60 to 70 percent range.
- Hardness
Hardness is the penetration resistance of the substance surface. Hardness tests evaluate the depth that a ball or cone-shaped object can be pressed into the surface of a material. The Brinell scale uses a 10 millimeter hardened steel ball to measure the width of the indentation, while the Rockwell method uses a diamond cone and measures depth of penetration.
Precipitation and martensitic hardening types can be hardened by heat treatment. Other types can be hardened via cold working.
- Tensile Strength
Typically, tensile strength is the only mechanical characteristic needed to define wire and bar and products. Similar substance types may be used at different tensile strengths for entirely different applications. The required tensile strength of wire and bar products directly related to the product’s final use, post fabrication.
Spring wire has the greatest tensile strength after fabrication. This strength is achieved by cold working the metal into rolled-up springs. The wire would not function as a spring without this great strength.
These high tensile strengths are not needed in wire used in forming or weaving processes. Bar or wire, used as the raw material for fasteners, such as screws and bolts, should be smooth enough shape into a head and threads, yet sufficiently strong to perform its intended function.
The families of stainless steel each have a range of yield and tensile strengths.
- High Temperatures
Stainless steel has superior performance to other carbon steels at high temperatures. They are more fire resistant, even at temperatures over 500° C, and they retain their stiffness more than carbon steel, even at temperatures above 300° C.
- Cryogenic Resistance
Some stainless steels excel at dealing with broad temperature ranges. Austenitic steels keep high tensile strength and exhibit exceptional toughness at sub-zero temperatures. This extends their range of use, and opens up new possibilities for modern applications.
Cryogenic temperatures are poorly managed by precipitation, martensitic, and ferritic steels, as their toughness dips with falling temperatures.
- Higher Work Hardening Ratios
The ability of a metal to increase its strength during the cold working process is a unique property of stainless steels, which can be annealed and cold worked to manipulate its strength to the desired level.
This implies that the same type of stainless steel can be used for multiple applications by simply changing its strength. For example, used as spring wire.
- Electrical Conductivity and Permeability
Stainless steel, like all metals, conducts electricity, although its electrical conductivity is poor compared to other metals such as copper, gold, and mercury.
Austenitic stainless steels are non-magnetic, although cold working can generate magnetic characteristics in some types. All the other classes possess magnetic properties.
Stainless Steel’s Chemical Properties
What makes stainless steel so unique and incredibly useful are its chemical properties.
- High Oxidation Resistance
This distinguishing characteristic of stainless steel is its versatility. One example is its resistance to oxidation because of its chromium content, which can rise to as much as 26 percent in some alloys.
Other metals must be guarded by anti-corrosion coatings, such as zinc, or by paints, but as these coatings wear away, corrosion sets in. Stainless steel, however, reacts to any damage or wear to its covering of chromium oxide by forming a new coat. This provides continuous corrosion resistance.
- Biologically Inert
Stainless steel does not react with biological material, making it the first choice for medical instruments, such as plates like trauma screws, and surgical instruments. This characteristic also makes it the best choice for cutlery and kitchen appliances.
- Acidic, Basic, And Organic Resistant
Stainless steel is resistant to a significant number of chemical compounds, organic compounds, acids and bases. Acid resistance differs from type to type, with some being highly resistant and other only resistant to low acidic concentrations.
They are similarly inert to organic and basic compounds, which makes stainless steel the ideal material for handling, storage, and chemical manufacture.
Stainless steel also resists salt, moisture, sulphur, chloride compounds, and carbon dioxide with ease, surviving in the harshest of environments for a longer period than other metals.
Other Properties (besides physical and chemical properties)
Characteristics are not limited to chemical and mechanical ones. The list below highlights other properties that make stainless steel a great choice for many other applications.
- Recyclability
Stainless steel is highly recyclable, making it an excellent choice for manufacturing new products. This reduces the strain on the environment by lowering waste and minimizing the exploitation of new raw materials.
It’s non-biodegradable, which stops it from polluting. It does not break down and seep into the water table.
- Easy to Work
Stainless steel is very workable, allowing designers to create complex products and shapes. Stainless steel bending, laser cutting, and CNC machining services, are all possible, with no need for exotic equipment.
- Easy to Maintain
Stainless steel products are readily cleaned with ordinary household cleaners, such as detergent, which keep them looking new and extend their service life.
In businesses where hygiene standards are elevated, and where electrical equipment is exposed to a humid or corrosive environments, stainless steel is often used.
This reduces replacement costs and makes an initially expensive purchase economical over time.
- Aesthetic Appeal
Stainless steel can achieve a high luster, so this metal is an excellent choice for highly visible surfaces. It comes in a variety of finishes from matte to bright. It can be engraved, tinted, embossed, and brushed.
In the next chapter, you will learn what elements are used as alloys to achieve these chemical, mechanical, and other properties.

Chapter Four: Which Elements Create the Properties of Stainless Steel
Various elements play crucial roles in the way stainless steels perform in terms of strength, mechanical, and chemical properties. Various stainless steel alloys are given a specific grade/type based upon their composition. The following text identifies those elements and explains the role played by each element.
The Elements
- Carbon
When carbon is added to iron the result is steel. The addition of carbon enhances iron’s hardness and strength. Heat treatment alone is insufficient to harden and strengthen pure iron. However, a broad spectrum of strength and hardness is achieved by adding carbon.
High carbon content is undesirable in austenitic and ferritic stainless steels, particularly for welding purposes, because the risk of carbide precipitation is exacerbated.
- Manganese
Hot working characteristics, hardenability, toughness, and strength are accomplished through the addition of manganese.
As with nickel, manganese is a key element in austenitic stainless steels, frequently used as an alternative for nickel in the AISI 200 series of austenitic stainless steels. One example includes AISI 202 as an alternative for AISI 304.
- Chromium
The addition of chromium enhances steel’s resistance to oxidation (rusting). As chromium content increases, higher resistance to oxidation is achieved.
Stainless steels contain no less than 10.5% chromium (often 11 or 12%), creating a exceptional level of corrosion resistance when compared to steels with lower chromium percentages.
Corrosion resistance is the beneficial by-product of a self-repairing, passive layer of chromium oxide, which forms on the stainless steel’s surface.
- Nickel
The presence of nickel, around 8 percent and greater, are present in high chromium stainless steels, creating a number of grades are both heat and corrosion-resistant.
These include austenitic stainless steels, such as 18-8 (304/1.4301). The ability of nickel to form austenitic steel results in an alloy that exhibits toughness, strength and resistance to oxidation and corrosion.
- Molybdenum
Molybdenum is an essential additive for stainless steels designed to resist pitting and crevice corrosion, especially in environments high in chlorides and sulfur.
- Nitrogen
Similar to nickel, nitrogen is crucial in creating austenitic stainless steel. When nitrogen is combined with stainless steel, yield strength is significantly improved, as is resistance to pitting corrosion.
- Copper
Copper is a common residual component of stainless steel. Copper is added to various alloys to produce properties such as precipitation hardening or enhanced corrosion resistance, predominantly in seawater and in the presence of sulfuric acid.
- Titanium
To stabilize carbide, titanium is added, particularly when the metal will be welded. Titanium interacts with carbon to form titanium carbides that are somewhat stable and cannot be smoothly melted in steel, which diminishes the phenomenon of intergranular corrosion.
By adding 0.25 to 0.60 percent titanium, the carbon merges with the titanium, unlike chromium, which prevents the corrosion-resistant chromium from being tied up as intergranular carbides which would cause the loss of corrosion resistance at the grain borders.
Titanium use has diminished because of steelmakers’ capacity to produce stainless steel with deficient carbon substances. Such steels are easily welded with no need for stabilization.
- Phosphorus
Phosphorus is usually added (along with sulfur) to enhance machinability. While phosphorus in austenitic stainless steel raises strength, it diminishes corrosion resistance, and also raises the material’s propensity to break during welding.
- Sulfur
Added in small amounts, sulfur improves machinability, but like phosphorus, it has a detrimental effect on weldability and corrosion resistance.
- Selenium
Selenium was formerly used as an additive to enhance machinability.
- Niobium (AKA Colombium)
Carbon stabilization is accomplished by adding niobium to steel and plays a similar role to titanium. Moreover, niobium strengthens steels and alloys for enhanced temperature service.
- Silicon
Silicon is typically used as a deoxidizing element in the steel melting procedure. A small quantity of silicon is used in most steels.
- Cobalt
When exposed to strong radiation, such as in a nuclear reactor, cobalt becomes extremely radioactive. Therefore, all stainless steels used in nuclear service will have cobalt content limitations of around 0.2 percent.
This is significant issue as some residual amount of cobalt is present in the nickel used to create austenitic stainless steel.
- Calcium
Added in small quantities, calcium improves machinability without any adverse effects on other properties induced by sulfur, selenium, and phosphorus.
In the next chapter, you will learn the advantages these elements provide stainless steel in the marketplace.

Chapter Five: The Characteristics and Advantages of Stainless Steel
Stainless steel is widely used in a variety of industries because it has a multitude of highly desirable features.
Many of these attributes are made possible by adding chromium, which, as we learned, makes steel up to two-hundred times more resistant to corrosion than with no chromium content.
Other desirable features for customers are its durability and strength, resistance to low and high-temperatures, ease of fabrication and high formability. Stainless steels are long-lasting, low maintenance, attractive in appearance, recyclable, and environmentally friendly. Stainless steel need not be coated, treated, or painted. The following list highlights stainless steel’s characteristics.
- Corrosion resistant
- High tensile strength
- Durable
- Hot & cold resistant
- Easy to form & and fabricate
- Low-maintenance
- Long service life
- Excellent aesthetics
- Recyclable & environmentally friendly
Top 12 Benefits of Stainless Steel
Stainless steel offers a multitude of benefits, such as corrosion resistance. strength, ease of fabrication, and so on. Let’s get into greater detail.
- Excellent Oxidation Resistance
It resists corrosion\rust because of its chromium alloy. Alloys with low chromium content can still resist corrosion in freshwater environments, while those with high chromium content are capable of resisting corrosion in acidic, saltwater, and chlorine rich environments. High chromium stainless steels also perform well in alkaline environments, making their characteristics useful in processing plants.
Used indoors or outdoors, the corrosion-resistant properties of stainless steel are unmatched. Moisture is everywhere and can cause rusting and tarnishing in other metals, but not stainless steel.
- Fire and Heat Resistant
The special high nickel and chromium alloys avoid scaling and maintain stainless steel’s durability at high temperatures. Stainless steel is used in boilers, pipelines, heat exchangers, valves, super-heaters, and aerospace and aircraft applications.
- Hygiene
Stainless steel is easily cleaned, and it can be sterilized with steam because of its corrosion resistance. This makes it the first choice for strict hygienic conditions such as kitchens, hospitals, and food processing plants.
- Aesthetic Appearance
Stainless steel offers outstanding aesthetics and a modern appearance.
- Strength-To-Weight Benefit
Because austenitic steels become stronger as they are worked, they allow thinner material to be used with no sacrifice of strength, which yields substantial cost savings.
- Ease of Fabrication
Modern steel-making methods permit stainless steel to be bent, cut, welded, machined, formed, and assembled more readily than other steels.
- Impact Resistance
The austenitic micro-pattern of the 300 series offers high strength at sub-zero temperatures, making these steels especially suited to cryogenic applications.
- Long-Term Value
When considering costs, production, material, and life cycle expenses, need to be considered. When these are taken into account, stainless steel usually comes out on top.
- 100 Percent Recyclable
Over 50 percent of the current stainless steel produced comes from recycled stainless steel.
- Choice of Finishes
Stainless steel is available in a wide array of finishes, providing significant flexibility in project design. Once stainless steel is formed to the required shape, thickness, and size, mill finishing can be used to enhance its attractiveness.
- Self-Healing
No, not a typo! Stainless steel can heal itself. The chromium within stainless steel create a thin layer of chromium oxide on the surface. If stainless steel is damaged, its exposure to the oxygen in the atmosphere causes the chromium oxide layer to be renewed. This doesn’t mean that extensive damage, such as crumpling or piercing, will repair miraculously, but it does mean that surface scrapes will heal because of the chromium oxide.
- Durability
Stainless steel is robust. Even thin stainless steel can support a significant amount of weight, not to mention hot and cold temperature extremes, and weather extremes.

Chapter Six: How Stainless Steel Is Made
The processes used to make stainless steel vary according to the grade being manufactured. Shape and performance factors result from several factors, such as how it is formed, how it is worked, and how it is finished, to name a few.
It all begins with a melted alloy, which is achieved in the following ways.
Creating the Alloy
Step 1: Melting
Stainless steel manufacturing starts by smelting scrap metals and alloys in an electric arc furnace (EAF). Powerful electrodes in the electric arc furnace heats the mixture to form a molten/liquid mixture. This can take several hours to accomplish.
Because stainless steel is highly recyclable; many stainless steel orders contain 60 percent recycled steel—great for the environment and cost effective.
Furnace temperatures can vary based upon the type of stainless steel being produced.
Step 2: Reducing Carbon Content
As we have learned, carbon enhances iron’s hardness and strength but, too much can cause issues, such as carbide precipitation during welding.
Before the molten stainless steel can be formed, the carbon content must be calibrated to match the specifications of the steel being produced.
The two methods foundries use to control carbon content of carbon are 1) argon oxygen decarburization (AOD) in which an argon gas mixture is injected into the molten steel to reduce the carbon content with minimal loss of other essential elements, and 2) vacuum oxygenation (VOD). In this method, oxygen is injected into the molten steel in a vacuum, which removes vented gases from the chamber and reduces the carbon content.
Using either of these methods allows precision control over carbon content and ensures a proper mixture that will produce the correct properties and characteristics in the final product.
Step 3: Tuning
Post carbon reduction, the manufacturer must ensure that equilibrium and homogeneity of chemistry and temperature have occurred in order to be certain that the metal will meet grade specifications.
Samples are taken, tested, and evaluated. Needed changes are made until the batch meets the standard.
Forming or Casting
The molten steel must then be formed, and the steel cooled. Various forms are used, and the choice depends upon the product the steel is intended to produce.
Common forms include:
- Billets
- Blooms
- Rods
- Slabs
- Tubes
An ID is attached to the form, allowing the batch to be tracked throughout subsequent processes.
These processes vary according to the grade, final product, or job. Slabs become sheets, strips, and plates. Billets and blooms become wires and bars.
Depending on the desired grade and shape, the steel will undergo multiple passes through the process needed to create the desired form and/or properties.
Common Processing Methods
- Hot Rolling
This is performed at temperatures exceeding the steel’s recrystallization temperature. This forms the coarse physical dimensions of the steel. Precise temperature control keeps the steel hot enough to work without changing its internal crystalline structure.
Constant passes are needed to adjust the dimensions of the steel. For example, passing
sheets through rollers to achieve a desired thickness.
- Cold Rolling
Usually used when precision is needed, cold rolling exists below the steel recrystallization temperature. Multiple backed rollers are used to form steel. This process creates a more uniform and attractive finish.
Cold rolling can the steel’s structure, making heat treatment a necessity to recrystallize the steel to its original state.
- Annealing
After rolling, many steels undergo an annealing procedure, which includes cycles of heating and cooling, which soften the steel and release internal stresses.
Duration and temperature is a function of the type of steel, and the effects on the final product.
- Descaling or Pickling
As steel is processed, scale builds on its surface.
This not only affects the aesthetics of the finished product, it can also compromise stain resistance, weldability, and durability. Eliminating scale is necessary so that the oxide barrier that provides stainless steel with its stain resistance and corrosion resistance can form successfully.
Picking or descaling removes scale by controlling heating and cooling in an oxygen free environment or through the use of an acid bath (known as acid pickling).
After descaling, the metal may return to an extrusion or rolling mill for further handling. The annealing process follows until the desired characteristics are attained.
- Cutting
When the steel has been worked, the batch is cut to match the order.
Mechanical cutting with circular knives, guillotine knives, and die punching are the most common methods.
However, for complex shapes, plasma cutting or flame cutting is frequently needed.
The choice depends on the steel’s grade and the form of the intended product.
- Finishing
Stainless steel comes in a variety of finishes. Finishing is the final step in the manufacturing process. A plethora of techniques are used in finishing stainless steel, including sandblasting, acid wash, belt grinding, and belt polishing.
At this point, the steel is ready for shipment to the customer. In the next chapter, we will discuss how businesses and the general public use stainless steel.

Chapter Seven: How Stainless Steel Is Used
Because stainless steels possess a huge number of attractive, useful properties, they are used prolifically in all walks of life. They are ubiquitous—and can be found in electronics, furniture, kitchen appliances, dining rooms, restaurants, equipment of all stripes, construction, the medical field, aircraft, motor vehicles of every kind, sporting equipment, and the list goes on.
- Springs (all types)
- Hose clamps
- Bottling machinery
- Conveyors
- Desalination equipment
- Jewelry
- Cryogenic components and vessels
- Dryers
- Mixing bowls
- Paper mill equipment
- Furnace parts
- Oil refining equipment
- Heat exchangers
- Dyeing equipment
- Textile industry
- Jet engine parts
- Dairy industry
- Fasteners
- Pipes
- Tubing
- Welded storage tanks for organic and non-organic chemicals
- Emission and burner control components
- Combustion chambers
- Skewers
- Furnace arch supports
- Bank vaults
- Kiln linings
- Glass molds
- Ductwork
- Fish hooks
- Coal chutes
- Cutlery
Wherever you cast your eye, you are likely to see stainless steel.

Chapter Eight: How to Choose the Right Stainless Steel for Your Purpose
I am frequently asked, “What grade of stainless steel should I choose?” In this chapter, I will answer that question.
Unfortunately, there is no single answer. The choice depends upon the application, on the environment, and on other key factors.
Although stainless steel is broadly used in a variety of industries, variables in strength, corrosion resistance, etc. make it understandable that choosing a particular series and grade can be a tough proposition.
However, the diversity of available stainless steels ensures your objectives are met and that everything will proceed as expected. Choosing correctly is just a matter of understanding your needs. In this chapter, we discuss the common needs that must be satisfied by making the correct choice.
Common Needs and the Stainless Steels that Meet Them
- The Amount and Type of Corrosion Resistance Desired
Many stainless steels are chosen for their ability to resist corrosion.
Consider the type and amount of corrosion resistance required. Stainless steels have a variety of corrosion resistant profiles. Austenitic stainless steels, for example, are highly corrosion resistant because of their high levels of chromium. Grade 304 would be a good choice if wear resistance is also a consideration. Grades 304 and 316 are comparable in terms of wear resistance, but grade 316 also contains molybdenum, which offers enhanced corrosion resistance.
If cost is a factor (and when is it not), you can compromise with a martensitic or ferritic stainless steel. However, they offer a lower level of corrosion resistance because the nickel and/or chromium content is low.
If stress and corrosion resistance parameters aren’t met by austenitic, ferritic, or martensitic alloys, you may choose a double-sided stainless steel.
- Operating Environment
To what environment will the stainless steel be exposed? This factor must be determined for you to make a good choice. Consider the environment in which your final product is used. While it may be alright to use stainless steel to manufacture a door frame in your office or home, ordinary stainless steel will not withstand high temperatures, low PH, crevice corrosion, and high stress levels.
Consider stainless steels in the austenitic T3XX Series, such as grades 316 and 304.
These stainless steels will keep their toughness, corrosion resistance, and strength properties over a range of temperatures. For example, type 316 will resist chloride ions that you get in chemical and marine processing applications.
Remember, not all grades of stainless steel can be welded. Stainless steels that do not resist stress corrosion cracking and hot cracking cannot be used for welding. For example, martensitic stainless steel has a high carbon content, making welds difficult. Avoid martensitic stainless steels when welding is a factor.
Grades like 304 or 304L have low carbon content compared to other stainless steel grades. Generally, austenitic stainless steels are best for forming and welding, although stress cracking can be an issue.
Duplex steels have excellent weldability and formability features, provided you choose the correct grade, grades 407 and 430, for example. Ferritic stainless steels can also be welded, but many grades of ferritic steel are incompatible with welding because of the hardness of heat-affected zones (HAZ). It can crack in certain temperature ranges.
- Mechanical Qualities
Toughness, yield strength, and ductility are crucial examples of the mechanical qualities you need to consider. Stainless steels range from 10 to 30 percent chromium. Keep top-of-mind that chromium is the corrosion resistant driver in any stainless steel series/grade. Chromium is the key to corrosion resistance.
In the austenitic series, the presence of nickel produces high ductility and toughness, while the most corrosion-resistant series/grades of stainless steel contain molybdenum, chromium, and nickel.
Your focus must extend beyond nickel content, however, because the method of treatment also has a significant effect on the metal’s mechanical properties.
The time the steel is held at various temperatures during the cooling process and the overall speed of cooling affects its mechanical properties. While heat treatment can enhance carbon steel’s hardness, you should remember that austenitic stainless steels are hardened via cold processes, which include bending, rolling, swaging, and drawing, all at temperatures less than the temperature of recrystallization.
It should also be noted that although cold processes improve hardness, they will reduce other characteristics, such as impact resistance and elongation.
- The Magnetic Response (Permeability)
Each stainless steel series/family has its own physical characteristics. The magnetic characteristics of stainless steel are a function of the alloy’s components.
Primary stainless steel exhibits a ferritic structure that is magnetic because of the addition of chromium. By adding carbon, it can be hardened—making it a martensitic stainless steel.
However, the most widely used stainless steels are austenitic because of their higher chromium content. The addition of nickel changes the steel’s physical structure and makes it non-magnetic.
Austenitic stainless has less magnetic interaction than ferritic. Grades of stainless steel rich in nickel content such as 310 or 316 grades are non-magnetic under any circumstance and these stainless steels are ideal for applications requiring a metal that is not magnetic. If you seek a stainless steel grade with a high magnetic response, choose the martensitic and ferritic stainless steel grades (400 series). It is classified as ferromagnetic and comes with high permeability, which is the measure of magnetization that a material obtains in response to an applied magnetic field.
Also, keep in mind that duplex series stainless steels, such as 2205 and 2101, when looking for magnetic grades of stainless steel.
Because there are so many stainless steel grades to choose from, you must decide which stainless steel grade you need to meet the demands of your application. By choosing the appropriate series and grade, you will complete your project successfully and save money.
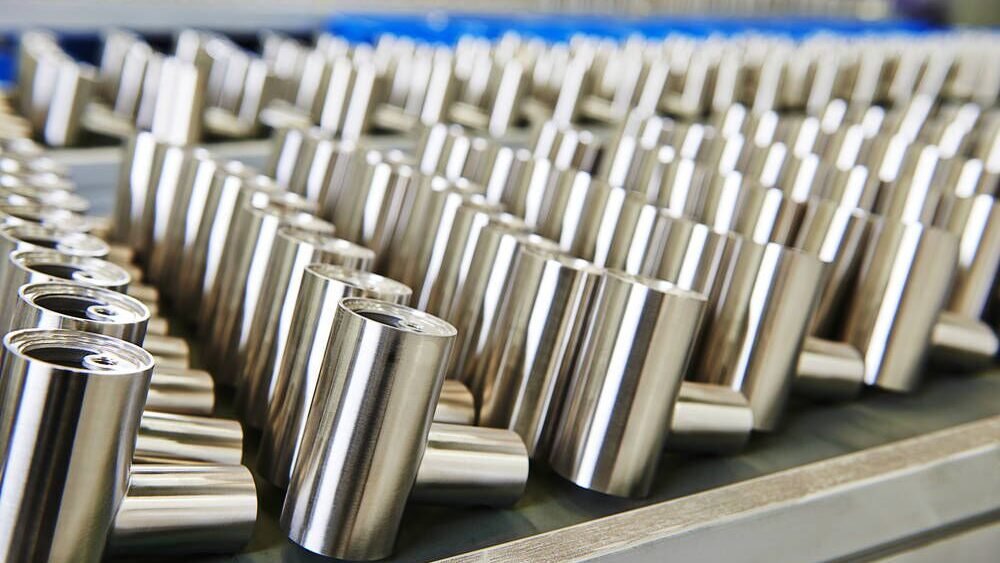
Conclusion
Stainless steel offers heat and corrosion resistance, besides the conventional characteristics of steel. In short, it provides the commonly known benefits of steel, plus unique ones that are not widely known. As we have learned, stainless steel has a longer service life, endures toxic environments, and resists the stresses of heat and cold better than steel.
Wear resistance depends on the grade. Abnormal ambient conditions such as poor air circulation, high salinity, and low oxygen levels may stain even stainless steel.
So, stainless steel isn’t perfect nor is it invincible, however, it is more than capable of meeting the challenges modern civilization puts to it.
The data within this guide is indicative only and should not be considered a substitute for the full specifications regarding these classes and grades. Notably, the parameters for mechanical properties can vary widely. The information within is based on current knowledge and is provided in good faith, but must not be regarded as a substitute for your own due diligence.
I hope you find this guide useful, and please, feel free to share it with your friends.