Metal stamping, a foundational process in manufacturing, has a myriad of applications. But where exactly do we see its influence? Let’s explore the diverse uses of metal stamping in our world.
Metal stamping is a technique where metal sheets are transformed into specific shapes using specialized tools. It’s primarily used for creating parts in industries like Consumer electronics, Medical, Aerospace, NEV, Communications, Industrial automation, and more.
Curious about the depth and breadth of metal stamping’s applications? Join us as we delve into its multifaceted uses.

Consumer Electronics
Gadgets and Devices
In today’s digital age, consumer electronics are an integral part of our daily lives. From smartphones and tablets to laptops and smartwatches, these gadgets are everywhere. But have you ever wondered how these devices achieve their sleek designs and precise functionality? Enter metal stamping. This manufacturing process plays a pivotal role in shaping the casings, buttons, and even some internal components of these devices. The precision and efficiency of metal stamping allow for the mass production of consistent and high-quality parts, ensuring that our gadgets are both aesthetically pleasing and functionally reliable.
Component Manufacturing
Beyond the visible exteriors of our electronic devices lie intricate circuits and components that power their operations. These components, often minuscule yet crucial, are crafted through precise metal stamping processes. Connectors, heat sinks, shields, and various other electronic components are stamped from metal sheets to exact specifications. This precision is vital, as even a slight deviation can impact the performance of the device. By ensuring that each component fits perfectly and functions as intended, metal stamping plays a silent yet indispensable role in the world of consumer electronics.

Medical Industry
Surgical Instruments
The medical field demands unparalleled precision, especially when it comes to tools used in surgeries and procedures. Metal stamping plays a critical role in the creation of many surgical instruments, from scalpels and forceps to clamps and retractors. These tools, often made from stainless steel or other biocompatible metals, are stamped to exact dimensions, ensuring their efficacy and safety during surgeries. The sharpness of a scalpel’s edge, the grip of a tweezer, or the curve of a surgical hook – all these are achieved through meticulous metal stamping, ensuring that medical professionals can rely on their tools even in the most critical situations.
Diagnostic Devices
Accurate diagnosis is the cornerstone of effective medical treatment. To achieve this, healthcare professionals rely on a range of diagnostic devices, many of which benefit from metal stamping. Components for devices like X-ray machines, MRI scanners, and even some parts of blood testing equipment are crafted using this process. The casings, brackets, and some internal components are stamped to perfection, ensuring the devices’ reliability and precision. In an industry where even the smallest error can have significant consequences, the precision and consistency offered by metal stamping are invaluable.

Aerospace
Aircraft Components
The aerospace industry, known for its rigorous standards and the need for precision, heavily relies on metal stamping for crafting various aircraft components. From the external skin of airplanes to the intricate parts of their engines, metal stamping ensures that each piece is crafted to exact specifications. The wings, fuselage panels, landing gear components, and even the tiny rivets holding them together are often products of this process. Given the extreme conditions these components are subjected to – from high altitudes to varying temperatures and pressures – the precision and durability ensured by metal stamping are paramount. It’s this meticulous attention to detail that ensures the safety and reliability of aircraft in flight.
Satellite Structures
Beyond our atmosphere, metal stamping plays a crucial role in space exploration, particularly in the construction of satellites. These celestial devices, tasked with communication, observation, or scientific research, are built to withstand the harsh conditions of space. Metal stamping is employed to create the satellite’s structural components, antenna dishes, and even some internal mechanisms. The process ensures that these parts are lightweight yet robust, capable of enduring the vacuum of space, extreme temperatures, and potential collisions with space debris. As we venture further into the cosmos, the precision and reliability of metal stamping continue to be instrumental in advancing our understanding of the universe.
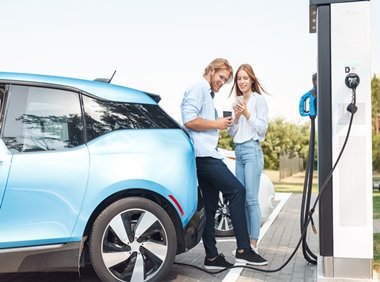
NEV (New Energy Vehicles)
Battery Components
As the world shifts towards sustainable transportation, New Energy Vehicles (NEVs) are at the forefront of this revolution. Central to the functioning of these vehicles are their batteries, which store and provide the necessary energy. Metal stamping plays a pivotal role in crafting various components of these batteries. From the battery casings that protect the cells to the connectors ensuring efficient energy transfer, each part is stamped to precision. This ensures optimal performance, safety, and longevity of the batteries, which are crucial for the overall efficiency and reliability of NEVs.
Structural Elements
The structural integrity of NEVs is of paramount importance, given the unique challenges they face, such as housing heavy battery packs. Metal stamping is extensively used to create various structural elements of these vehicles. From the chassis that forms the vehicle’s backbone to the body panels that shape its exterior, metal stamping ensures that each component is robust, lightweight, and designed for maximum efficiency. The process allows for intricate designs and shapes, catering to the aerodynamic needs of NEVs, ensuring they are both aesthetically pleasing and functionally optimized for their electric propulsion.

Communications
Network Equipment
In our interconnected world, seamless communication is vital. At the heart of this global connectivity lies an intricate web of network equipment, facilitating data transfer across continents in mere milliseconds. Metal stamping plays an integral role in crafting many components of this equipment. Routers, switches, modems, and base stations, to name a few, contain parts shaped and formed through metal stamping. These components, whether they’re connectors, casings, or internal circuitry mounts, are crafted to exact specifications, ensuring reliable data transmission and minimizing potential disruptions in our digital communications.
Device Casings
Our communication devices, from smartphones to tablets and laptops, are our gateways to the digital world. Protecting the delicate electronics within these gadgets are their casings, many of which owe their form and function to metal stamping. These protective shells, often made of aluminum or other metals, are stamped to precision, ensuring a snug fit for the internal components. Beyond protection, these casings are also designed for aesthetics and ergonomics, with metal stamping allowing for intricate designs, sleek finishes, and durable structures that can withstand the rigors of daily use.

Industrial Automation
Machinery Parts
As industries evolve, the push for efficiency and precision has led to a surge in automation. Central to this transformation are machines that operate with minimal human intervention. Metal stamping is instrumental in crafting various parts of these machines. From gears and levers to casings and mounts, each component is stamped to exact dimensions, ensuring smooth operation. The precision offered by metal stamping ensures that these parts fit seamlessly, reducing wear and tear and prolonging the machinery’s lifespan. In an environment where even a minor malfunction can lead to significant downtimes, the reliability offered by stamped components is invaluable.
Control Systems
Beyond the mechanical components, industrial automation relies heavily on control systems to regulate and oversee operations. These systems, often a blend of electronics and mechanics, contain numerous parts crafted through metal stamping. Enclosures that house delicate electronics, connectors that facilitate communication between different parts of a system, and even some sensor components are products of the stamping process. These elements, while often overlooked, are critical in ensuring that the control systems function optimally, allowing industries to maintain consistent quality, efficiency, and safety in their automated processes.

Conclusion
Metal stamping, a seemingly simple yet profoundly intricate process, has woven its way into the fabric of modern manufacturing. Its influence is seen everywhere, from the gadgets we use daily to the vehicles we drive, and even the machines that produce other products. Its precision and efficiency have made it an indispensable tool in industries ranging from consumer electronics to aerospace, medical, communications, and industrial automation.
The versatility of metal stamping allows it to cater to the unique demands of each industry, ensuring products are not only functional but also durable and aesthetically pleasing. As we’ve journeyed through its various applications, it’s evident that metal stamping is more than just a manufacturing process; it’s an art form that combines technical prowess with creative ingenuity.
In an era where quality, efficiency, and sustainability are paramount, metal stamping stands out as a beacon of modern manufacturing excellence. As industries continue to evolve, the role of metal stamping will undoubtedly remain pivotal, driving innovation and shaping the future of production.